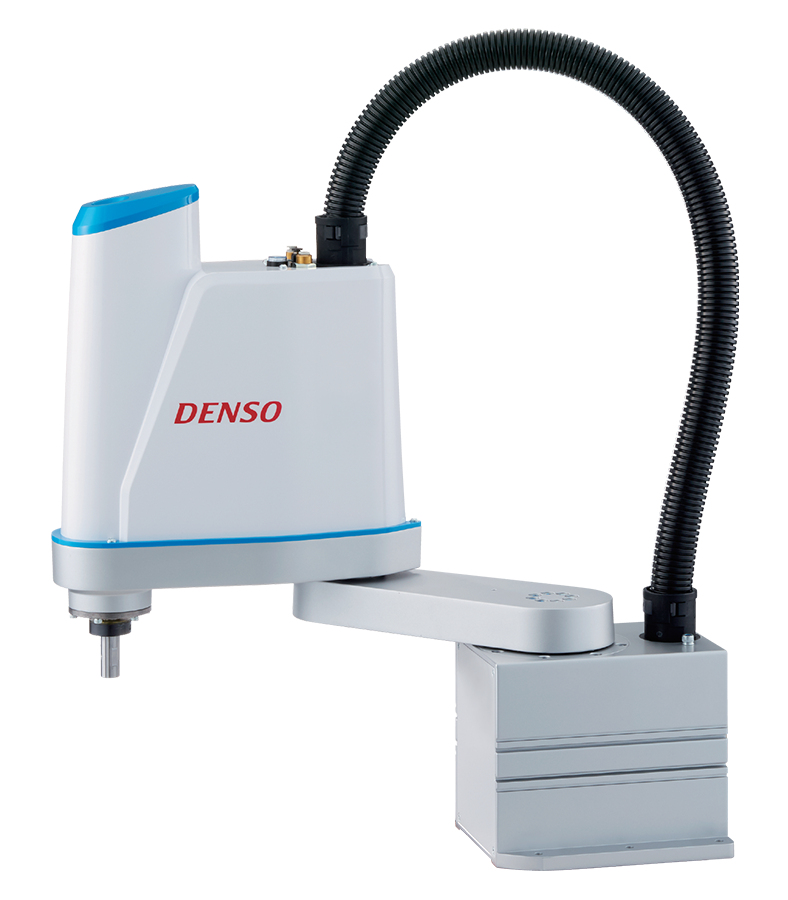
The high-performance, competitively-priced LPH-040 4-axis SCARA robot is an excellent choice for users who are new to automation. Compact and lightweight, LPH-040 handles lighter duty applications with ease, such as electronics, assembly, and pick-and-place to name a few. The LPH is a perfect option for first-time buyers looking to reduce start-up costs for projects that require a shorter, three- to five-year duty lifecycle.
Max Payload |
Reach |
Cycle Time |
Repeatability |
3kg |
400mm |
0.45sec |
±0.020mm |
Overview
- High-performance
- Competitively priced
- Compact and lightweight
Gripper Design with High Degree of Freedom
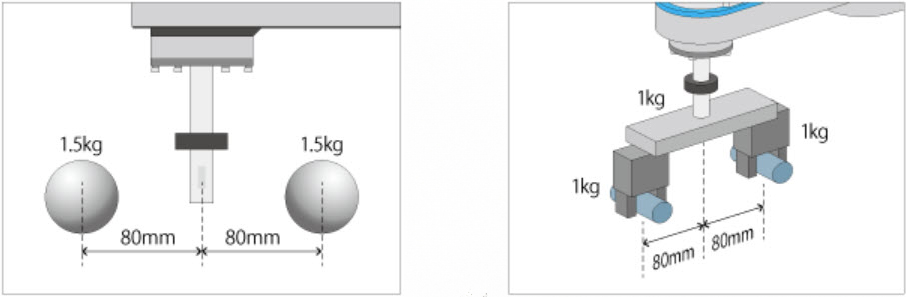
The maximum moment of inertia of the T-axis is large in order to provide a gripper design with a high degree of freedom.
* Also supports use in other configurations including in an overhanging position.
Reduction in Work Time without the Use of PLC
The robot and surrounding equipment can be controlled together according to the purpose through use of the high-performance controller RC8 function. This feature realizes a total cost down for equipment.
Enables Control from PLC with No Programming Knowledge Required
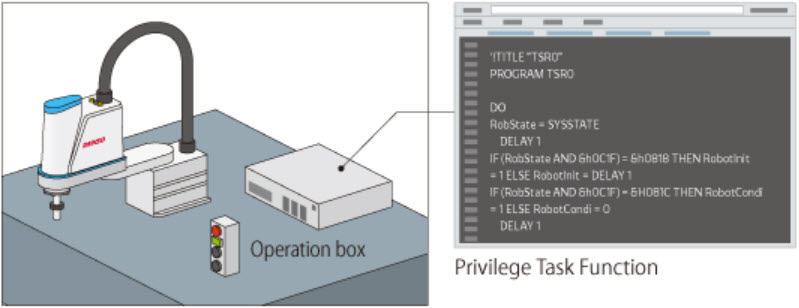
Specifications
Model name | LPH040A1*1 | |
No. of axes | 4 | |
Position detection | Absolute encoder | |
Drive motor | AC servomotors for all joints | |
Brakes | Brakes for Z axis | |
Overall arm length (first arm+second arm) | 400mm (200mm+200mm) | |
Motion angle and stroke | J1 (1st Axis) | ±130° |
J2 (2nd Axis) | ±146.6° | |
Z (3rd Axis) | 150mm | |
T 4th Axis) | ±360° | |
Axis combination | J1 + J2 + Z + T | |
Maximum payload | 3kg | |
Cycle time *2 | 0.4 sec | |
Maximum composite speed (at the center of an end-effector mounting face) | At the center of the hand mounting flange | 4,710mm/s |
Z | 1,250mm/s | |
T | 1,875°/s | |
Position repeatability (at the center of an end-effector mounting face) *3 | J1+J2 | ±0.02mm |
Z | ±0.02mm | |
T | ±0.01° | |
Maximum force-fit | 45N (downward, for up to 1 sec) | |
Maximum allowable moment of inertia | 0.075kgm² | |
User air pipe | 3 systems (φ4x2, φ6x1) | |
User signal line | 15 (for proximity sensor signals, etc.) | |
Air source | Operating pressure | 0.05 - 0.35 MPa |
Max. allowable pressure | 0.6 MPa | |
Approximate weight | 16kg | |
1 Not available in all countries. | ||
2 Time required for a robot to move a 2kg payload between two points 300 mm apart at a height of 25mm. | ||
3 Position repeatability is the precision at constant ambient temperature. |
Downloads
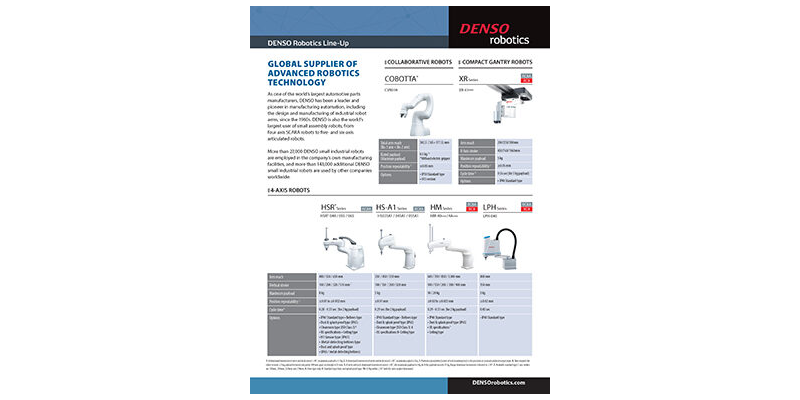
Robot Series Product Sheet
Overview of all DENSO robots
- Version
- Download 1316
- File Size 0.00 KB
- File Count 1
- Create Date June 9, 2022
- Last Updated January 16, 2024
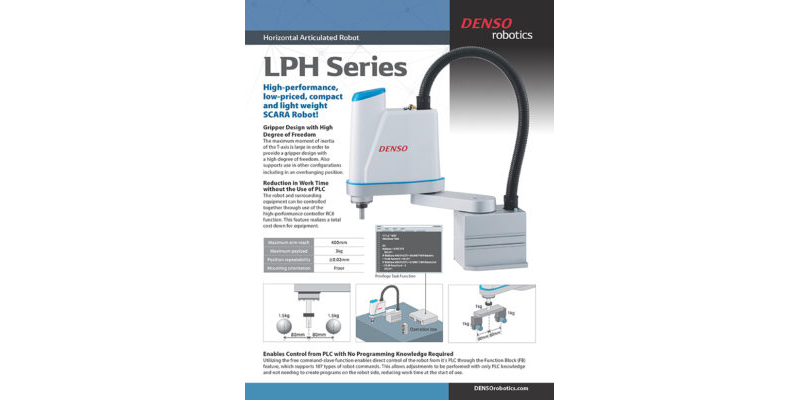
LPH Series Product Sheet
Two-page product sheet with features, characteristics and specs.
- Version
- Download 146
- File Size 0.00 KB
- File Count 1
- Create Date October 15, 2021
- Last Updated June 9, 2022
CAD Files and Manuals
Find 2D/3D CAD data, application software, PDF manuals, and part lists. (Account registration required)
Online/Interactive Manuals
Account registration required.