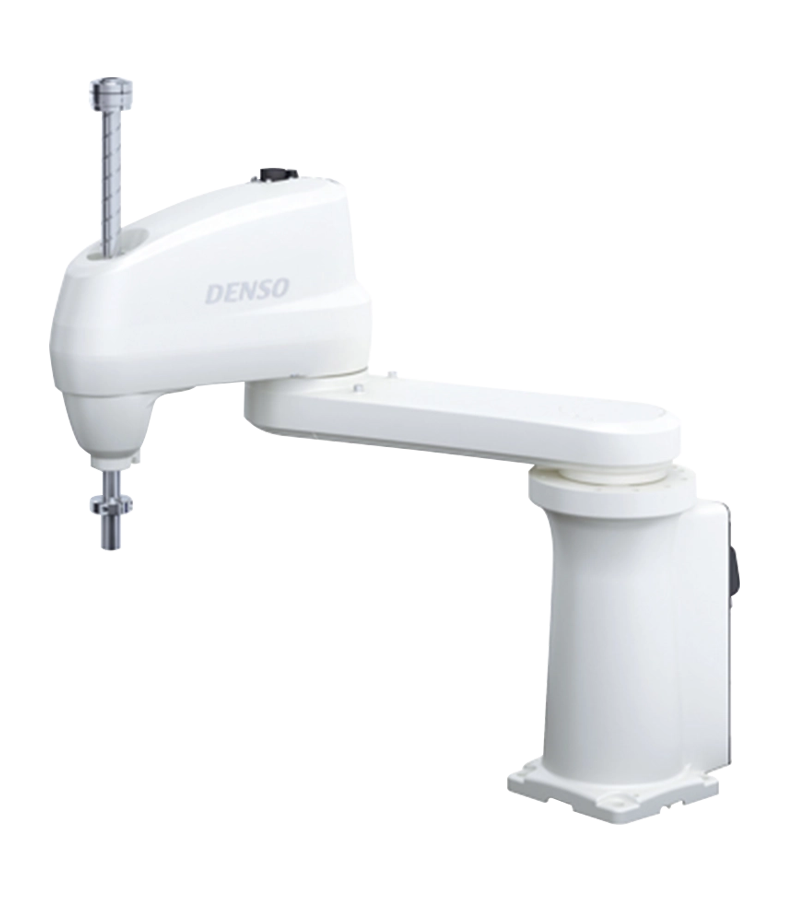
The HS-A1 Series compact, 4-axis SCARA robots offer the highest speed and repeatability in their class. Although these small industrial robots have a compact, space-saving design, they have a large load-handling capability, with a maximum payload of 5 kg. In addition, their large, 0.1 kgm2 maximum allowable moment of inertia enables a wide range of end effectors and applications. All HS-A1 Series robots are available in dust- and mist-proof (IP65) or ISO 4 (class 10) cleanroom configurations. ANSI and CE compliance allows global deployment. UL-listed models are available for both the U.S. and Canada.
Max Payload |
Reach |
Cycle Time |
Repeatability |
5kg |
350-550mm |
0.35sec |
±0.015/±0.020mm |
Overview
- Outstanding speed and repeatability
- Compact, space-saving design
- High maximum moment of inertia (0.1 kgm²) allows wide range of end effectors and applications
Model Name |
Payload |
Arm Length |
Basic Cycle Time* |
Position Repeatability |
HS035A1-N* |
5 kg |
350 mm |
0.35 sec. |
±0.015 mm |
HS045A1-N* |
5 kg |
450 mm |
0.35 sec. |
±0.020 mm |
HS055A1-N* |
5 kg |
550 mm |
0.35 sec. |
±0.020 mm |
Choice of Configurations
- Basic (IP20)
- Dust and Mistproof (IP65)
- Cleanroom (Class 10)
Powerful
One of the highest applicable maximum moments of inertia in their class.
Overhead Mountable
450 and 550 mm reaches.
ANSI/CE Compliant and UL Listed
ANSI and CE compliance allows global deployment. UL-listed models are available for both the U.S. and Canada.
Specifications
Base Models
Model name *2 | HS035A1-N/* | HS045A1-N/* | HS055A1-N/* | |
No. of axes | 4 | 4 | 4 | |
Position detection | Absolute encoder | Absolute encoder | Absolute encoder | |
Drive motor | AC servomotors for all joints | AC servomotors for all joints | AC servomotors for all joints | |
Brakes | Brakes for Z axis and T axis | Brakes for Z axis and T axis | Brakes for Z axis and T axis | |
Overall arm length (first arm+second arm) | 350mm (125mm+225mm) | 450mm (225mm+225mm) | 550mm (325mm+225mm) |
|
Motion angle and stroke | J1 (1st Axis) | ±155° | ±155° | ±155° |
J2 (2nd Axis) | ±145° | ±145° | ±145° | |
Z (3rd Axis) * | *10: 100mm *15: 150mm *20: 200mm *32: 320mm | *10: 100mm *15: 150mm *20: 200mm *32: 320mm | *10: 100mm *15: 150mm *20: 200mm *32: 320mm |
|
T (4th Axis) | ±360° | ±360° | ±360° | |
Maximum payload | 5kg | 5kg | 5kg | |
Maximum composite speed (at the center of an end-effector mounting face) | 7,200mm/sec | 6,300mm/sec | 7,100mm/sec | |
Z | 2,000mm/sec | 2,000mm/sec | 2,000mm/sec | |
T | 2,400°/sec | 2,400°/sec | 2,400°/sec | |
Cycle time *3 | 0.29 sec | 0.29 sec | 0.29 sec | |
Position repeatability(at the center of an end-effector mounting face) *4 | J1+J2 | ±0.015mm | ±0.02mm | ±0.02mm |
Z | ±0.01mm | ±0.01mm | ±0.01mm | |
T | ±0.005° | ±0.005° | ±0.005° | |
Maximum force-fit | 98N (1 sec or less) | 98N (1 sec or less) | 98N (1 sec or less) | |
Maximum allowable inertia moment (inertia) | 0.1kgm² | 0.1kgm² | 0.1kgm² | |
User air piping | 4 systems (φ4x2, φ6x2) | 4 systems (φ4x2, φ6x2) | 4 systems (φ4x2, φ6x2) | |
User signal line | 19 (for proximity sensor signals, etc.) | 19 (for proximity sensor signals, etc.) | 19 (for proximity sensor signals, etc.) | |
Air source | Operating pressure | 0.05 - 0.35 MPa | 0.05 - 0.35 MPa | 0.05 - 0.35 MPa |
Maximum allowable pressure | 0.59 MPa | 0.59 MPa | 0.59 MPa | |
Noise | <80 dB(A) | <80 dB(A) | <80 dB(A) | |
IP classification | IP65 (Option) | IP65 (Option) | IP65 (Option) | |
Cleanroom classification | Class 3 (Option) | Class 3 (Option) | Class 3 (Option) | |
Approximate weight | 25kg | 25kg | 25kg | |
*1 The data listed on this page is for standard models. For other options, please contact us here. | ||||
*2 An asterisk [*] in a model name indicates Z-axis stroke. | ||||
*3 Time required for a robot to move a 2kg payload between two points 300mm apart at a height of 25mm. | ||||
*4 Position repeatability is the precision at constant ambient temperature. |
Standard Models
Model name *2 | HS035A1-N* | HS045A1-N* | HS055A1-N* | |
No. of axes | 4 | 4 | 4 | |
Position detection | Absolute encoder | Absolute encoder | Absolute encoder | |
Drive motor and brake | AC servomotors for all joints | AC servomotors for all joints | AC servomotors for all joints | |
Brakes | Brakes for Z axis and T axis | Brakes for Z axis and T axis | Brakes for Z axis and T axis | |
Overall arm length (first arm+second arm) | 350mm (125mm+225mm) | 450mm (225mm+225mm) | 550mm (325mm+225mm) | |
Motion angle and stroke | J1 (1st Axis) | ±155° | ±155° | ±155° |
J2 (2nd Axis) | ±145° | ±145° | ±145° | |
Z (3rd Axis) * | *10: 100mm *15: 150mm *20: 200mm *32: 320mm | *10: 100mm *15: 150mm *20: 200mm *32: 320mm | *10: 100mm *15: 150mm *20: 200mm *32: 320mm |
|
T (4th Axis) | ±360° | ±360° | ±360° | |
Axis combination | J1 +J2 + Z +T | J1 +J2 + Z +T | J1 +J2 + Z +T | |
Maximum payload | 5kg | 5kg | 5kg | |
Maximum composite speed (at the center of an end-effector mounting face) | 7,200mm/s | 6,300mm/s | 7,100mm/s | |
Z | 2,000mm/s | 2,000mm/s | 2,000mm/s | |
T | 2,400°/s | 2,400°/s | 2,400°/s | |
Cycle time *3 | 0.29 sec | 0.29 sec | 0.29 sec | |
Position repeatability (at the constant ambient temperature) *4 | J1+J2 | ±0.015mm | ±0.02mm | ±0.02mm |
Z | ±0.01mm | ±0.01mm | ±0.01mm | |
T | ±0.005° | ±0.005° | ±0.005° | |
Maximum force-fit | 98N (1 sec or less) | 98N (1 sec or less) | 98N (1 sec or less) | |
Maximum allowable inertia moment | 0.1kgm² | 0.1kgm² | 0.1kgm² | |
Brake releasing | Non UL-Listed models | Press the brake release switch in the direct teaching mode. Enter a brake release command with the teach pendant or mini-pendant. | Press the brake release switch in the direct teaching mode. Enter a brake release command with the teach pendant or mini-pendant. | Press the brake release switch in the direct teaching mode. Enter a brake release command with the teach pendant or mini-pendant. |
UL-Listed models | Press the brake release switch when the controller power is ON. The teach pendant or mini-pendant cannot release the brakes. | Press the brake release switch when the controller power is ON. The teach pendant or mini-pendant cannot release the brakes. | Press the brake release switch when the controller power is ON. The teach pendant or mini-pendant cannot release the brakes. |
|
User air piping | 4 systems (φ4x2, φ6x2) | 4 systems (φ4x2, φ6x2) | 4 systems (φ4x2, φ6x2) | |
User signal line | 19 (for proximity sensor signals, etc.) | 19 (for proximity sensor signals, etc.) | 19 (for proximity sensor signals, etc.) | |
Air source | Operating pressure | 0.05 – 0.35 MPa | 0.05 – 0.35 MPa | 0.05 – 0.35 MPa |
Maximum allowable pressure | 0.59 MPa | 0.59 MPa | 0.59 MPa | |
IP classification | IP65 | IP65 | IP65 | |
Cleanroom classification (14644-1) | ISO 3 | ISO 3 | ISO 3 | |
Noise | <80 dB(A) | <80 dB(A) | <80 dB(A) | |
Approximate weight | 25kg | 25kg | 25kg | |
*1 See the name plate on each model. | ||||
*2 An asterisk [*] in a model name indicates Z-axis stroke | ||||
*3 Time required for a robot to move a 2 kg payload between two points 300 mm apart at a height of 25 mm. | ||||
*4 Position repeatability is the precision at constant ambient temperature. |
Overhead Mount Models
Model name | HS045A1-S* | HS055A1-S* | |
No. of axes | 4 | 4 | |
Position detection | Absolute encoder | Absolute encoder | |
Drive motor | AC servomotors for all joints | AC servomotors for all joints | |
Brake | Brakes for Z axis and T axis | Brakes for Z axis and T axis | |
Overall arm length (first arm+second arm) | 450mm (225mm+225mm) | 550mm (325mm+225) |
|
Motion angle and stroke | J1 (1stAxis) | ±152° | ±155° |
J2 (2nd Axis) | ±141° | ±145° | |
Z (3rd Axis) * | *10: 100mm *15: 150mm *20: 200mm *32: 320mm | *10: 100mm *15: 150mm *20: 200mm *32: 320mm |
|
T (4th Axis) | ±360° | ±360° | |
Axis combination | J1 + J2 + Z +T | J1 + J2 + Z +T | |
Maximum payload | 5kg | 5kg | |
Maximum composite speed | At the center of the hand mounting flange | 6,300mm/s | 7,100mm/s |
Z | 2,000mm/s | 2,000mm/s | |
T | 2,400°/s | 2,400°/s | |
Position repeatability (Value at the constant ambient temperature) | J1+J2 | ±0.02mm | ±0.02mm |
Z | ±0.01mm | ±0.01mm | |
T | ±0.005° | ±0.005° | |
Maximum force-fit | 98N (1 sec or less) | 98N (1 sec or less) | |
Maximum allowable inertia moment | 0.1kgm² | 0.1kgm² | |
Brake releasing | Models except UL-Listed ones | Press the brake release switch in the direct teaching mode. | Press the brake release switch in the direct teaching mode. |
Enter a brake release command with the teach pendant or mini-pendant. | Enter a brake release command with the teach pendant or mini-pendant. | ||
User air piping | 4 systems (φ4x2, φ6x2) | 4 systems (φ4x2, φ6x2) | |
User signal line | 19 (for proximity sensor signals, etc.) | 19 (for proximity sensor signals, etc.) | |
Air source | Operating pressure | 0.05 - 0.35 MPa | 0.05 - 0.35 MPa |
Maximum allowable pressure | 0.59 MPa | 0.59 MPa | |
IP classification | IP65 | IP65 | |
Noise | <80 dB(A) | <80 dB(A) | |
Approximate weight | 25kg *2 | 25kg *2 | |
*1 Overhead-mount type robots cannot be installed on the floor to work facing upward. | |||
*2 See the name plate on each model |
Downloads
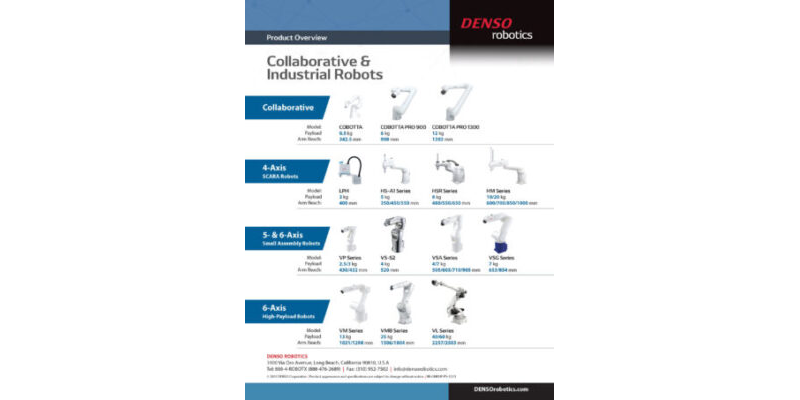
Collaborative & Industrial Robots Lineup Card
- Version
- Download 0
- File Size 4.00 KB
- File Count 1
- Create Date May 1, 2025
- Last Updated May 1, 2025
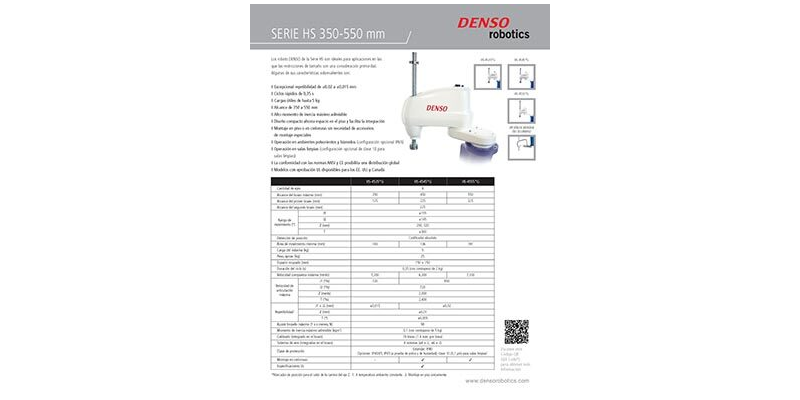
Hoja de producto de la serie HS (Spanish)
Ficha de producto de dos páginas con características, especificaciones y dimensiones.
- Version
- Download 52
- File Size 0.00 KB
- File Count 1
- Create Date October 15, 2021
- Last Updated October 15, 2021
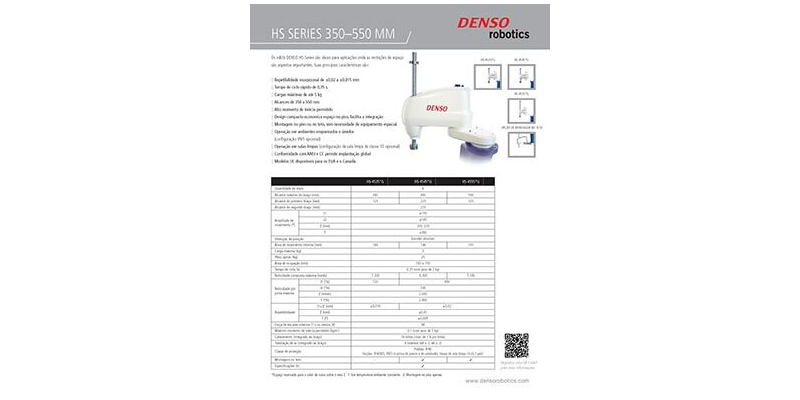
Folha de produto da série HS (Portuguese)
Folha de produto de duas páginas com características, especificações e dimensões.
- Version
- Download 17
- File Size 0.00 KB
- File Count 1
- Create Date October 15, 2021
- Last Updated October 15, 2021
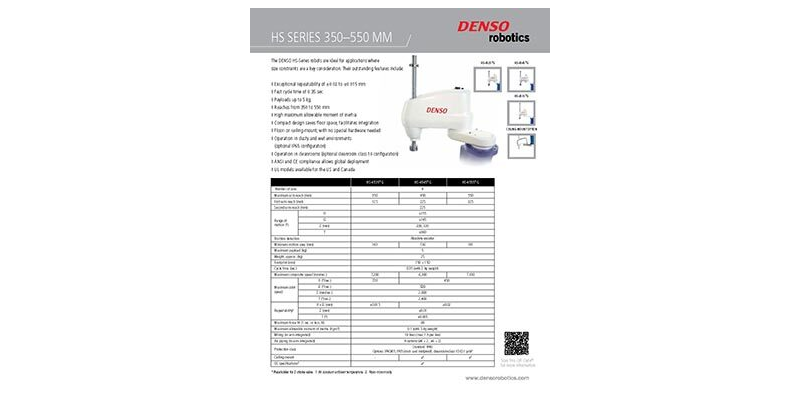
HS Series Product Sheet
Two-page product sheet with features, specifications and dimensions.
- Version
- Download 255
- File Size 0.00 KB
- File Count 1
- Create Date October 15, 2021
- Last Updated October 15, 2021
CAD Files and Manuals
Find 2D/3D CAD data, application software, PDF manuals, and part lists. (Account registration required)
Online/Interactive Manuals
Account registration required.