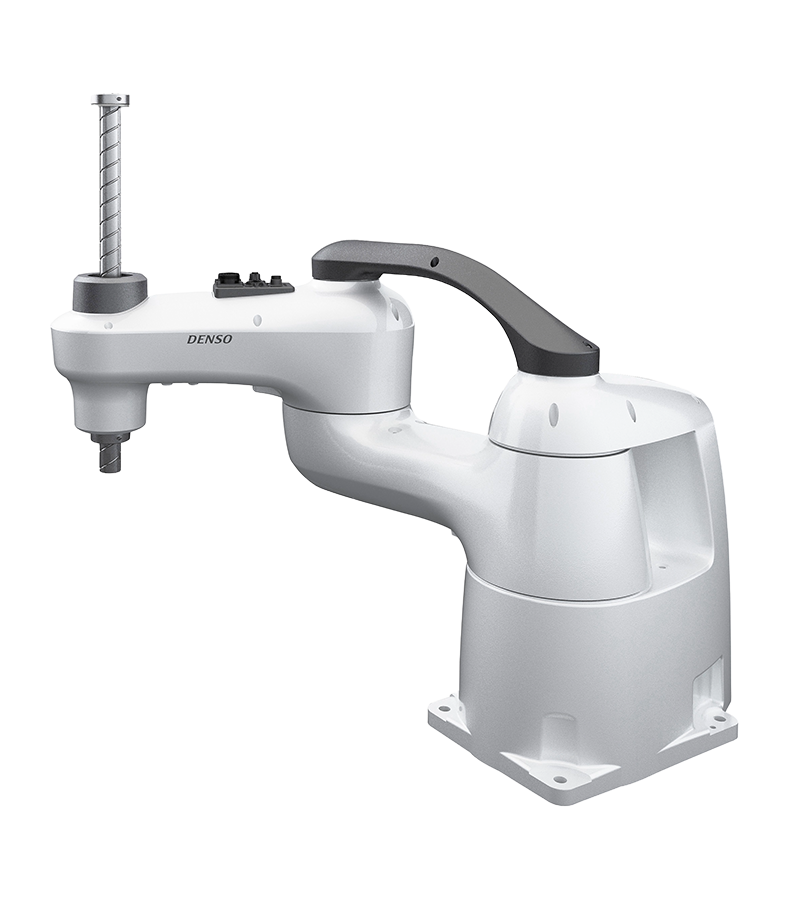
The HSR Series uses advanced vibration control, a newly designed, highly-rigid lightweight arm and improved heat dissipation in the base unit to achieve new levels of continuous high-speed performance and repeatability.
Max Payload |
Reach |
Cycle Time |
Repeatability |
8kg |
480-650mm |
0.28-0.31sec |
±0.010/±0.012mm |
Overview
- Quick Acceleration
- Runs continuously at high speed
- Stops precisely
Performance that Changes Everything
Reduced shaft whip and settling time, along with a lighter-weight arm and an optimized arm structure make the HSR robots more efficient than previous models, enabling them to accelerate faster, run continuously at their maximum rated speed and stop more precisely. Standard cycle time (with a 2 kg weight) is from 0.28 to 0.31 sec. and repeatability is from ±0.01 to ±0.012 mm. Maximum payload capacity is 8 kg, with available reaches of 480, 550, and 650 mm. Applications include high-speed, high-precision pick and place in assembly processes, as well as packaging processes in the food, medical device, pharmaceutical and cosmetics sectors.
Features
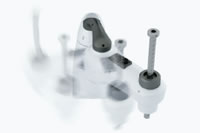
High-Speed Motion
Optimized Acceleration and Motion profiles
Improved high-speed motion results in more cycles per minute (CPM) and therefore higher productivity.
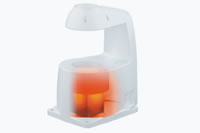
Continuous Motion
Achieving Continuous, Non-stop Motion
Improved heat dissipation in the base unit allows the robot to run continuously at its highest rated speed, a requirement in today’s demanding processes.
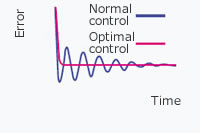
Vibration Control
Vibration-control Technique for Suppressing Vibrations
The robot quickly suppresses vibrations by actively reflecting the status of the arm to the controller’s vibration control. Vibrations that occur during high-speed transfer as well as residual vibrations are both suppressed, reducing cycle times.
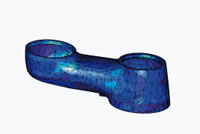
Lightweight
Newly designed, highly rigid lightweight arm
The combination of high rigidity and light weight allow the robot to handle a high payload of 8 kg and achieve high-speed motion at the same time.
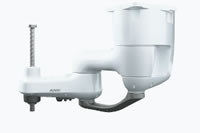
Flexible Mounting Configuration
The HSR robot is available in both floor- and ceiling-mount models.
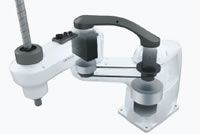
Optimum Layout
Optimized arm design allows the robot to achieve continuous high-speed motion
A large-capacity motor is integrated into the base unit. Weight reduction of the arm and an optimized arm design allow the robot to achieve its continuous high-speed performance.
Options
Wiring Protection Kit
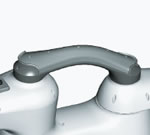
Protects external wiring to prevent cables from becoming unorganized, avoiding the risk of broken wires.
Built-in Ethernet
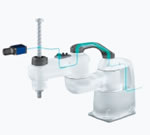
An Ethernet cable is built into the body and is easily connectable to external devices. Ethernet connectors (sold separately) are available as options.
External Battery
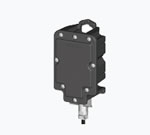
The encoder backup battery is installed outside the robot, facilitating maintenance and replacement of batteries.
Stopper with Bearing
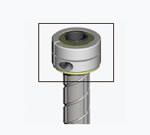
Protects wiring installed through the hole of the bearing located at the top of the Z-axis shaft.
Specifications
Standard Models
Model name | HSR048A1-N/S* | HSR055A1-N/S* | HSR065A1-N/S* | |
No. of axes | 4 | 4 | 4 | |
Position detection | Absolute encoder | Absolute encoder | Absolute encoder | |
Drive motor | AC servomotors for all axes | AC servomotors for all axes | AC servomotors for all axes |
|
Brakes | Brakes for Z and T axes | Brakes for Z and T axes | Brakes for Z and T axes | |
Overall arm length (first arm+second arm) | 480mm (205mm+275mm) | 550mm (275mm+275mm) | 650mm (375mm+275mm |
|
Motion angle and stroke | J1 (1st Axis) | ±130° | ±130° | ±130° |
J2 (2nd Axis) | ±143.5° | ±150° | ±150° | |
Z (3rd Axis) * | *10: 100mm *20: 200mm *32: 320mm *51: 510mm | *10: 100mm *20: 200mm *32: 320mm *51: 510mm | *10: 100mm *20: 200mm *32: 320mm *51: 510mm |
|
T (4th Axis) | ±360° | ±360° | ±360° | |
Axis combination | J1 + J2 + Z + T | J1 + J2 + Z + T | J1 + J2 + Z + T | |
Maximum payload | Z and T | 8kg | 8kg | 8kg |
Maximum composite speed | At the center of the hand mounting flange | 7,540mm/s | 8,000mm/s | 8,850mm/s |
Z | 100mm: 1,700mm/s 200mm: 2,300mm/s 320mm: 2,475mm/s | 100mm: 1,700mm/s 200mm: 2,300mm/s 320mm: 2,475mm/s | 100mm: 1,700mm/s 200mm: 2,300mm/s 320mm: 2,475mm/s |
|
T | 2,500°/s | 2,500°/s | 2,500°/s | |
Position repeatability (value at the constant ambient temperature.) | J1+J2 | ±0.01mm | ±0.012mm | |
Z | ±0.01mm | ±0.01mm | ±0.01mm | |
T | ±0.004° | ±0.004° | ±0.004° | |
Maximum force-fit | 98N (1 sec or less) | 98N (1 sec or less) | 98N (1 sec or less) | |
Maximum allowable inertia moment | 0.12kgm² | 0.12kgm² | 0.12kgm² | |
Brake releasing | Models except UL-Listed ones | 1. Press the brake release switch in the direct teaching mode. 2. Enter a brake release command with the teach pendant or mini-pendant. | 1. Press the brake release switch in the direct teaching mode. 2. Enter a brake release command with the teach pendant or mini-pendant. | 1. Press the brake release switch in the direct teaching mode. 2. Enter a brake release command with the teach pendant or mini-pendant. |
UL-Listed models | 1. Press the brake release switch when the controller power is ON. 2. The teach pendant or mini-pendant cannot release the brakes. | 1. Press the brake release switch when the controller power is ON. 2. The teach pendant or mini-pendant cannot release the brakes. | 1. Press the brake release switch when the controller power is ON. 2. The teach pendant or mini-pendant cannot release the brakes. |
|
User air piping | 4 systems (φ4×2, φ6×2) | 4 systems (φ4×2, φ6×2) | 4 systems (φ4×2, φ6×2) | |
User signal lines | ・19 (for proximity sensor signals, etc.) ・Ethernet (8) *1 | ・19 (for proximity sensor signals, etc.) ・Ethernet (8) *1 | ・19 (for proximity sensor signals, etc.) ・Ethernet (8) *1 |
|
Air source | Operating pressure | 0.05 - 0.35 MPa | 0.05 - 0.35 MPa | 0.05 - 0.35 MPa |
Max. allowable pressure | 0.59 MPa | 0.59 MPa | 0.59 MPa | |
Noise | <80 dB(A) | <80 dB(A) | <80 dB(A) | |
Approximate weight *2 | 31kg | 31.5kg | 32kg | |
*1 Option | ||||
*2 See the name plate on each model. |
Bellows Models
Model name | HSR048A1-N/S* | HSR055A1-N/S* | HSR065A1-N/S* | |
No. of axes | 4 | 4 | 4 | |
Position detection | Absolute encoder | Absolute encoder | Absolute encoder | |
Drive motor | AC servomotors for all axes | AC servomotors for all axes | AC servomotors for all axes |
|
Brakes | Brakes for Z and T axes | Brakes for Z and T axes | Brakes for Z and T axes | |
Overall arm length (first arm+second arm) | 480mm (205mm+275mm) | 550mm (275mm+275mm) | 650mm (375mm+275mm) |
|
Motion angle and stroke | J1 (1st Axis) | ±130° | ±130° | ±130° |
J2 (2nd Axis) | ±143.5° | ±150° | ±150° | |
Z (3rd Axis)* | *17: 170mm *29: 290mm *45: 450mm | *17: 170mm *29: 290mm *45: 450mm | *17: 170mm *29: 290mm *45: 450mm |
|
T (4th Axis) | ±360° | ±360° | ±360° | |
Axis combination | J1 + J2 + Z +T | J1 + J2 + Z +T | J1 + J2 + Z +T | |
Maximum payload | 8kg | 8kg | 8kg | |
Maximum composite speed (at the center of the hand mounting flange) | 7,540mm/s | 8,000mm/s | 8,850mm/s | |
Z | 170mm: 2,250mm/s 290mm: 2,475mm/s | 170mm: 2,250mm/s 290mm: 2,475mm/s | 170mm: 2,250mm/s 290mm: 2,475mm/s |
|
T | 2,500°/s | 2,500°/s | 2,500°/s | |
Position repeatability (value at the constant ambient temperature.) | J1+J2 | ±0.01mm | ±0.012mm | |
Z | ±0.01mm | ±0.01mm | ±0.01mm | |
T | ±0.004° | ±0.004° | ±0.004° | |
Maximum force-fit | 98N (1 sec or less) | 98N (1 sec or less) | 98N (1 sec or less) | |
Maximum allowable inertia moment | 0.12kgm² | 0.12kgm² | 0.12kgm² | |
Brake releasing | Models except UL-Listed ones | 1. Press the brake release switch in the direct teaching mode. 2. Enter a brake release command with the teach pendant or mini-pendant. | 1. Press the brake release switch in the direct teaching mode. 2. Enter a brake release command with the teach pendant or mini-pendant. | 1. Press the brake release switch in the direct teaching mode. 2. Enter a brake release command with the teach pendant or mini-pendant. |
UL-Listed models | 1. Press the brake release switch when the controller power is ON. 2. The teach pendant or mini-pendant cannot release the brakes. | 1. Press the brake release switch when the controller power is ON. 2. The teach pendant or mini-pendant cannot release the brakes. | 1. Press the brake release switch when the controller power is ON. 2. The teach pendant or mini-pendant cannot release the brakes. |
|
User air piping | 4 systems (φ4x2, φ6x2) | 4 systems (φ4x2, φ6x2) | 4 systems (φ4x2, φ6x2) | |
User signal lines | ・19 (for proximity sensor signals, etc.) ・Ethernet (8) *1 | ・19 (for proximity sensor signals, etc.) ・Ethernet (8) *1 | ・19 (for proximity sensor signals, etc.) ・Ethernet (8) *1 |
|
Air source | Operating pressure | 0.05 - 0.35 MPa | 0.05 - 0.35 MPa | 0.05 - 0.35 MPa |
Max. allowable pressure | 0.59 MPa | 0.59 MPa | 0.59 MPa | |
Noise | <80 dB(A) | <80 dB(A) | <80 dB(A) | |
Approximate weight *2 | 31kg | 31.5kg | 32kg | |
*1 Option | ||||
*2 See the name plate on each model. |
Downloads
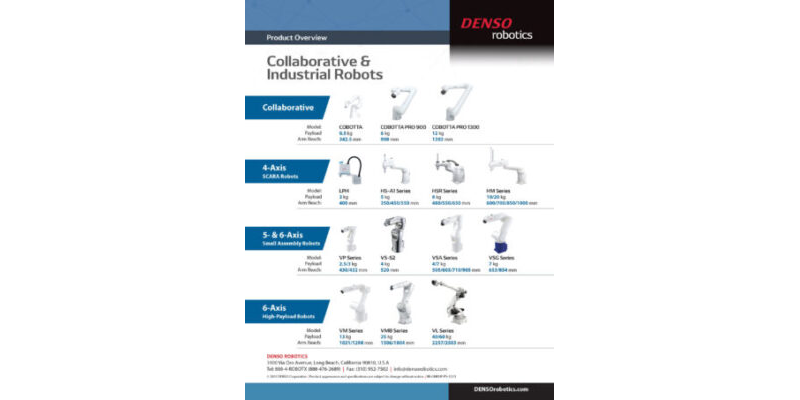
Collaborative & Industrial Robots Lineup Card
- Version
- Download 0
- File Size 4.00 KB
- File Count 1
- Create Date May 1, 2025
- Last Updated May 1, 2025
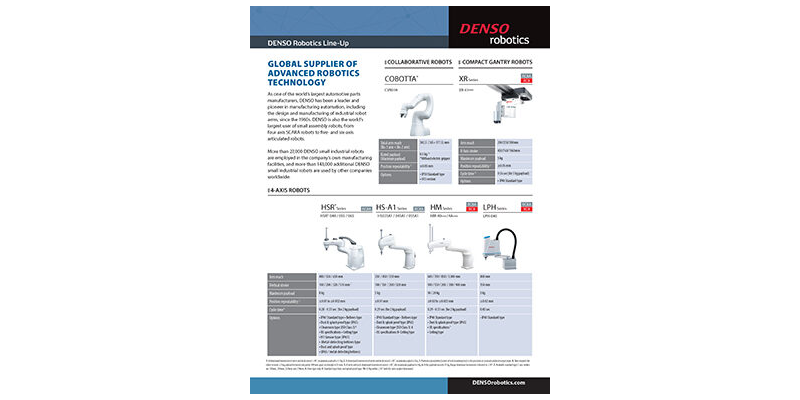
Robot Series Product Sheet
Overview of all DENSO robots
- Version
- Download 1318
- File Size 0.00 KB
- File Count 1
- Create Date June 9, 2022
- Last Updated January 16, 2024
CAD Files and Manuals
Find 2D/3D CAD data, application software, PDF manuals, and part lists. (Account registration required)
Online/Interactive Manuals
Account registration required.