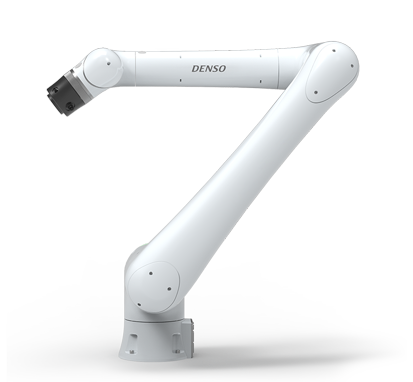

A high-speed collaborative robot engineered for productivity and safety.
The COBOTTA PRO is designed not only to facilitate collaboration between human workers and robots but also to consistently maximize productivity. It delivers a blend of productivity and safety for both simple tasks and multi-step processes like assembly and inspection work.
Max Payload |
Reach |
Position Repeatability |
6/12kg |
900/1300mm |
±0.03/±0.04mm |
Overview
Functional Safety
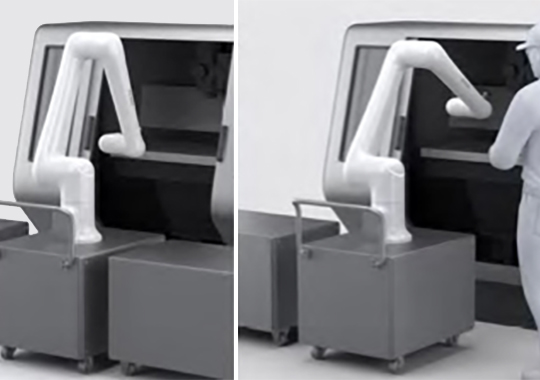
Functional safety designed to consistently maximize productivity while collaborating with human workers.
The COBOTTA PRO delivers a mix of productivity and safety by maximizing its operating speed when no workers are nearby while minimizing the distance needed to slow or stop when workers approach. When not collaborating with human workers, the unit operates at a maximum TCP speed of 2,500 mm/s with repeatability of ±0.04 mm. The COBOTTA PRO safeguards worker safety by augmenting proprietary torque sensors, which are standard equipment at each axis, with functional safety like torque, speed, and area monitoring. In addition, a touch-sensing soft cover that embeds high-sensitivity contact sensors in a silicon cushioning material further reduces collision risk. This design helps improve productivity safely.
Ease of Use and Precision
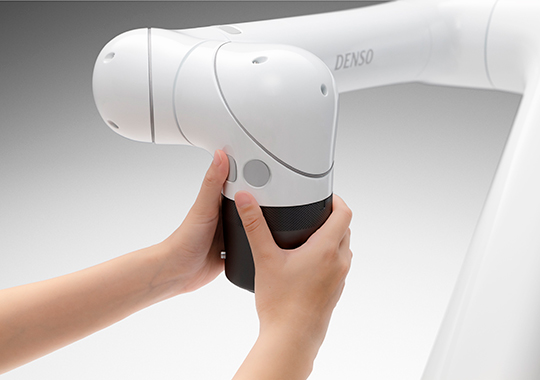
A development environment that’s easy for everyone.
We developed a new concept in direct teaching so the COBOTTA PRO can be used to quickly and easily automate complex tasks that require a high level of precision, for example, assembly work. Functionality accommodates a variety of teaching situations, from track memorization to fine-tuning down to 0.1 mm. In addition, the robot is built with Blockly as a new development environment. Utilized in conjunction with direct teaching, this approach lets even novice programmers implement high-precision, difficult applications like assembly processes intuitively and visually.
Automating Work
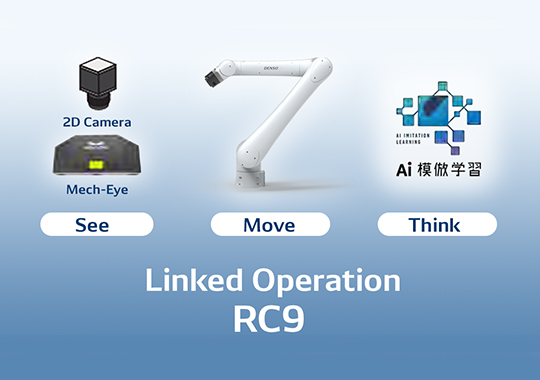
Automating work that conventionally has depended on human workers with a robot that sees, thinks, and moves like a person.
Collaborative robots are often used as an alternative means of performing work usually performed by human workers. Automating such work has been a challenging process that requires advanced technologies and expertise so that robots can see, think, and move like humans. Highly difficult work like assembly processes can be automated by using tools like Mech-Eye, a high-precision 3D image recognition camera, and AI Imitative Learning, a general-purpose AI software that automates tasks performed by human workers that are difficult to verbalize, to implement integrated control of the COBOTTA PRO and peripherals using the RC9 controller.
© 2023 DENSO. All Rights Reserved. COBOTTA is a registered trademark of DENSO Corporation. All other marks are owned by their respective companies and are used for reference purposes only.
Model name | COBOTTA PRO 900 | COBOTTA PRO 1300 | |
No. of axes | 6 | 6 | |
Position detection | Absolute encoder | Absolute encoder | |
Drive motor | AC servo motors for all axes | AC servo motors for all axes | |
Brakes | Brakes for all axes | Brakes for all axes | |
Overall arm length (first arm+second arm) | 900mm | 1,300mm | |
Maximum motion area (Point P: 4th, 5th, 6th axis center) | 908mm | 1,304mm | |
Maximum arm reach | 1,066mm | 1,463mm | |
Maximum motion angle | 1st axis | ±270° | ±270° |
2nd axis | ±150° | ±150° | |
3rd axis | ±150° | ±150° | |
4th axis | ±270° | ±270° | |
5th axis | ±150° | ±150° | |
6th axis | ±360° | ±360° | |
Maximum payload | 6kg | 12kg | |
Maximum speed in a collaborative state | Without touch-sensing soft cover | 1,800mm/s | 1,800mm/s |
With touch-sensing soft cover (optional) | 2,000mm/s | 2,000mm/s | |
Maximum TCP translational speed in a non-collaborative state | 2,100mm/s | 2,500mm/s | |
Position repeatabilty (at the center of a tool mounting face in each of X, Y and Z directions *1 | ±0.03mm | ±0.04mm | |
Maximum allowable moment | Around 4th axis | 20 N•m | 38.5 N•m |
Around 5th axis | 14.6 N•m | 28 N•m | |
Around 6th axis | 6.5 N•m | 12 N•m | |
Maximum allowable moment of inertia | Around 4th axis | 0.8kgm² | 1.45kgm² |
Around 5th axis | 0.45kgm² | 0.9kgm² | |
Around 6th axis | 0.1kgm² | 0.35kgm² | |
Connector panel mounting position | Back side of the robot base (bottom side of the robot base is optional) | Back side of the robot base (bottom side of the robot base is optional) | |
Equipment for Tool | Signal line: 2 pins (for Air Piping type), | Signal line: 2 pins (for Air Piping type), | |
8 pins (for Through Wiring type) *2 | 8 pins (for Through Wiring type) *2 | ||
Ethernet cable: 1 cable (8 pins) *3 | Ethernet cable: 1 cable (8 pins) *3 | ||
Analog input: 2 systems RS-485: 1 system | Analog input: 2 systems RS-485: 1 system |
||
Hand input: 5 pins / Hand output: 5 pins | Hand input: 5 pins / Hand output: 5 pins | ||
Lighting: 1 system | Lighting: 1 system | ||
Power source + (switching between OFF, 12 V and 24 V), Power source - (0 V) | Power source + (switching between OFF, 12 V and 24 V), Power source - (0 V) | ||
Air piping for user | φ4x2 (for Air Piping type) | φ4x2 (for Air Piping type) | |
Environment conditions of installation site (during operation) | Without touch-sensing soft cover | Ambient temperature:0 to 50° C | Ambient temperature:0 to 50° C |
With touch-sensing soft cover (optional) | Ambient temperature:5 to 45° C | Ambient temperature:5 to 45° C | |
Relative Humidity: 20 to 90% (No dew condensation allowed.) Vibration: <4.9m/s² (0.5G) | Relative Humidity: 20 to 90% (No dew condensation allowed.) Vibration: <4.9m/s² (0.5G) |
||
Pollution degree (IEC 60664-1) | 3 | 3 | |
Applicable standards | ISO 10218-1:2011 | ISO 10218-1:2011 | |
ISO 13849-1:2015 | ISO 13849-1:2015 | ||
ISO/TS 15066:2016 | ISO/TS 15066:2016 | ||
IEC 60204-1:2016/A1:2021 | IEC 60204-1:2016/A1:2021 | ||
EN 61000-6-2:2005 | EN 61000-6-2:2005 | ||
EN 61000-6-4:2007/A1:2011 | EN 61000-6-4:2007/A1:2011 | ||
EN 61000-6-7:2015 | EN 61000-6-7:2015 | ||
Air source | Operating pressure | 0 - 0.39 MPa | 0 - 0.39 MPa |
Maximum allowable pressure | 0.49 Mpa | 0.49 Mpa | |
Noise | <65 dB(A) | <65 dB(A) | |
IP classification | IP54 | IP54 | |
Cleanroom classification (ISO14644-1) | Class 5 | Class 5 | |
Approximate weight | 29kg | 41kg | |
*1 Precision figures assume use at a constant ambient temperature. | |||
*2 Choose either the air piping type or the through wiring type. | |||
*3 The Ethernet cable connected to the connector panel must be 20m or less in length. |
Downloads
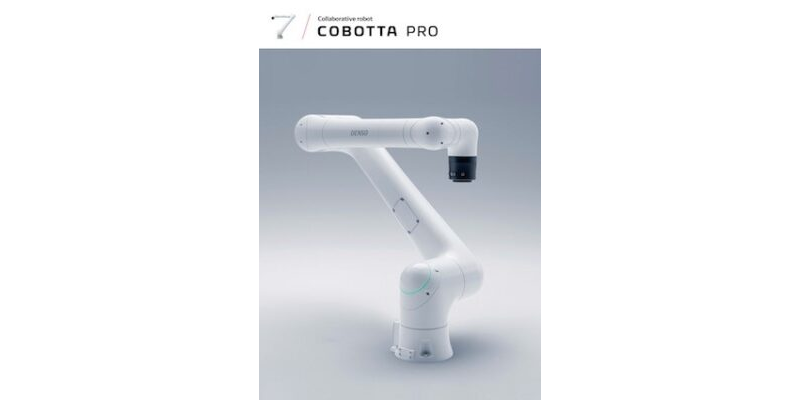
COBOTTA PRO Collaborative Robot Brochure
12-page product sheet with features, specifications and dimensions.
- Version
- Download 189
- File Size 0.00 KB
- File Count 1
- Create Date May 22, 2023
- Last Updated May 22, 2023
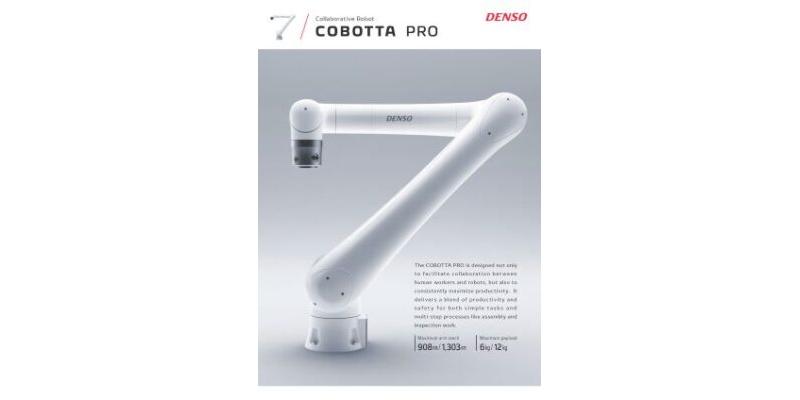
COBOTTA PRO Collaborative Robot Product Sheet
Two-page product sheet with features, specifications and dimensions.
- Version
- Download 97
- File Size 0.00 KB
- File Count 1
- Create Date May 8, 2023
- Last Updated May 8, 2023
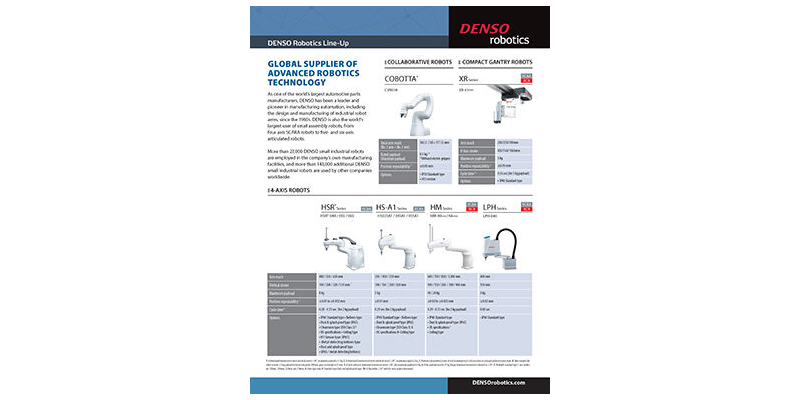
Robot Series Product Sheet
Overview of all DENSO robots
- Version
- Download 1063
- File Size 0.00 KB
- File Count 1
- Create Date June 9, 2022
- Last Updated January 16, 2024
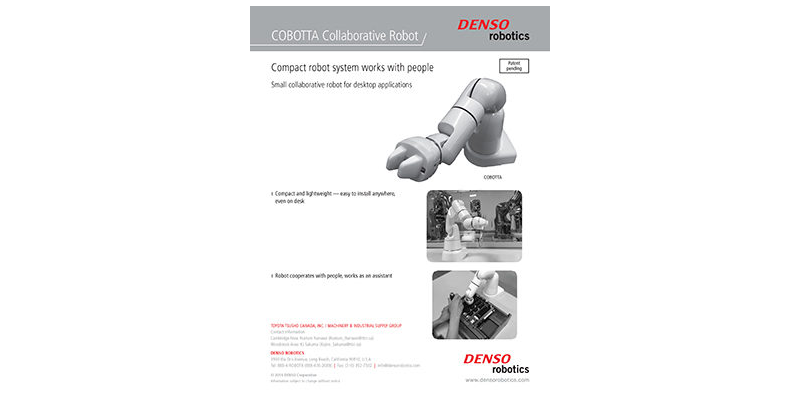
COBOTTA Collaborative Robot Product Sheet
Two-page product sheet with features, specifications and dimensions.
- Version
- Download 71
- File Size 0.00 KB
- File Count 1
- Create Date October 15, 2021
- Last Updated October 15, 2021
CAD Files and Manuals
Find 2D/3D CAD data, application software, PDF manuals, and part lists. (Account registration required)
Online/Interactive Manuals
Account registration required.