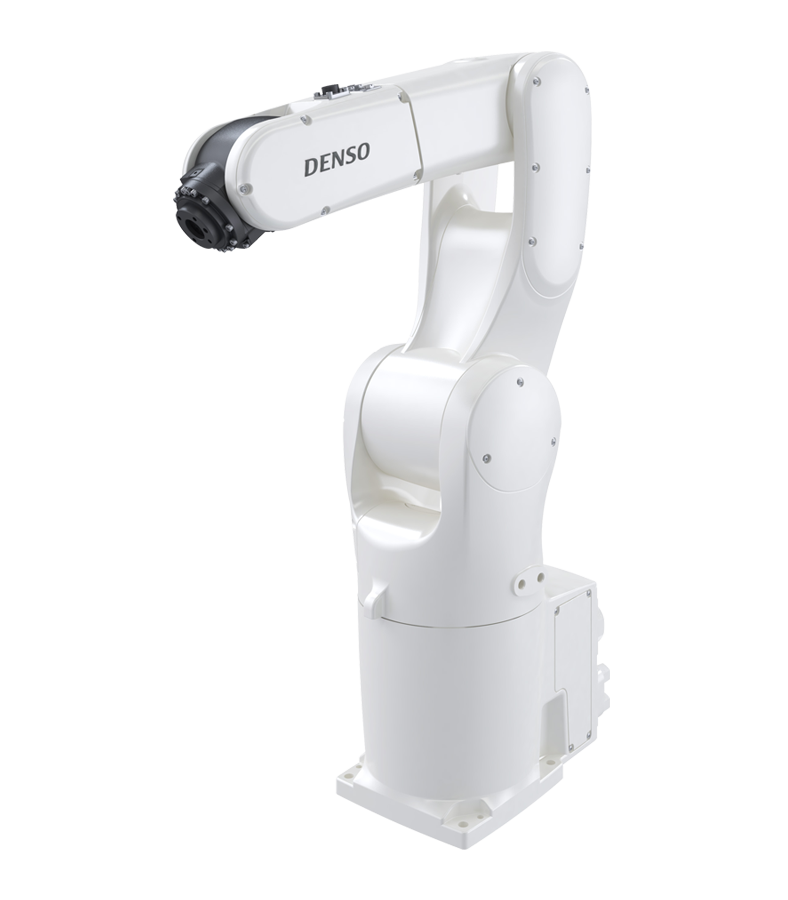
The VSA Series 6-axis articulated robots offer the world’s highest speed and precision for their class. Their design, which is even more compact than previous models, features ultraslim arms to facilitate integration and an optional bottom-side cable connection that saves valuable floor space. The robots can be mounted on the floor, ceiling or wall with no special hardware needed. An extremely high maximum allowable moment of inertia enables more flexible end-effector designs and a wider range of applications than conventional robots. In addition, a new internal wiring option allows users to easily connect Gigabit Ethernet devices and servo grippers directly to the flange, preventing cables from becoming tangled or interfering with peripheral equipment. A IP67 dust- and waterproof protection option enables the robots to resist cutting chips and high-pressure washing, extending their application range. Standard and cleanroom models are also available. ANSI and CE safety compliance allows global deployment.
Max Payload |
Reach |
Cycle Time |
Repeatability |
4-7kg |
505-905mm |
0.31/0.35sec |
±0.020/±0.030mm |
Overview
- High speed — world’s fastest in their class
- Outstanding repeatability
- High payload capacity
- Even more compact design
Reach |
Cycle Time* |
Repeatability |
505 mm |
0.37 sec. |
±0.020 mm |
605 mm |
0.37 sec. |
±0.020 mm |
710 mm |
0.33 sec. |
±0.020 mm |
905 mm |
0.36 sec. |
±0.030 mm |
1,000 mm |
0.31 sec. |
±0.025 mm |
**With 1 kg payload
Compact Design
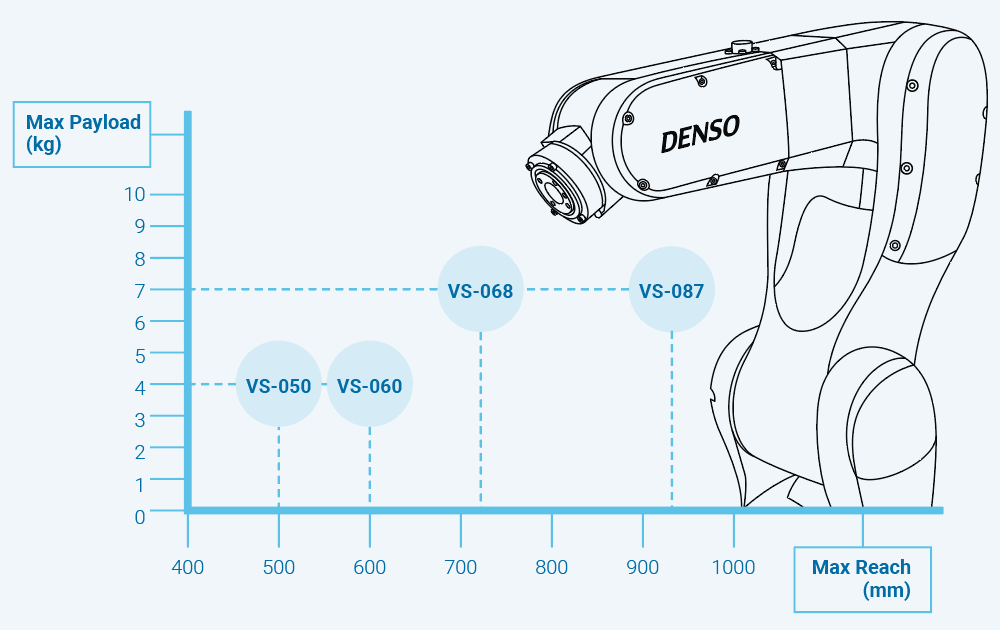
Maximum Arm Width
With a compact wrist unit can also afford to operate in narrow frontage.
- VS 050/060 – 193 mm
- VS 068/087 – 235 mm
Maximum Wrist Width
Compact body with few projections and depressions. Neat installations without interfering with surrounding items.
- VS 050/060 – 95 mm
- VS 068/087 – 100 mm
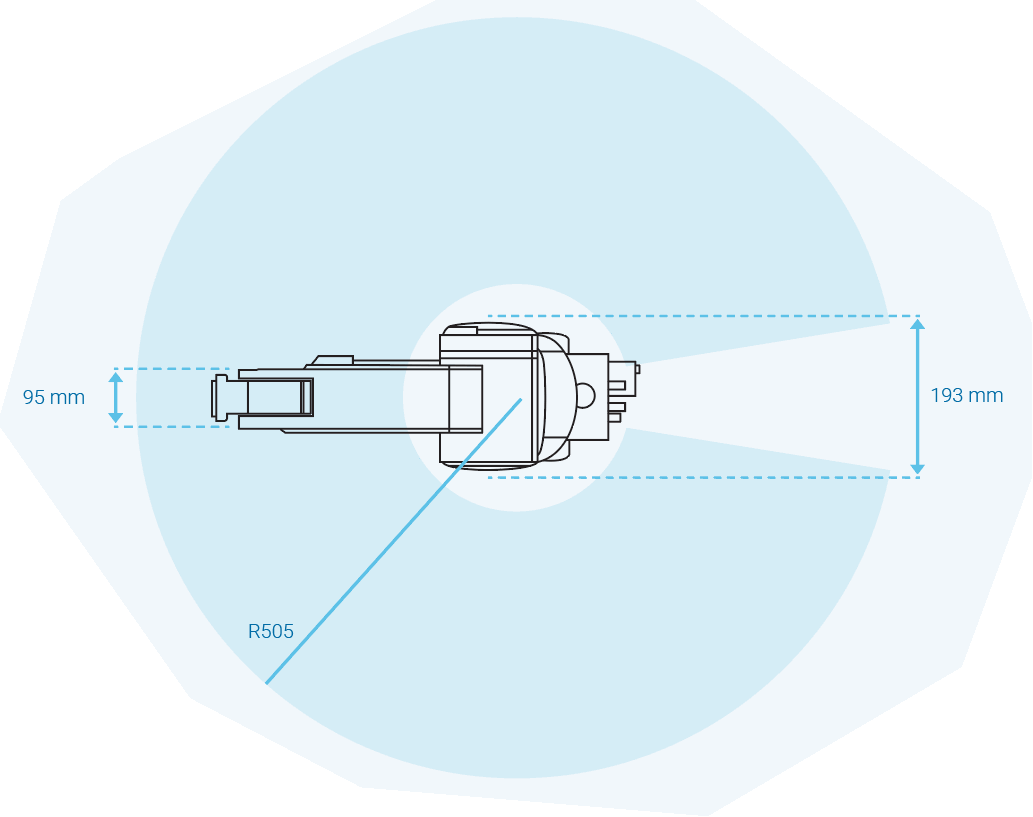
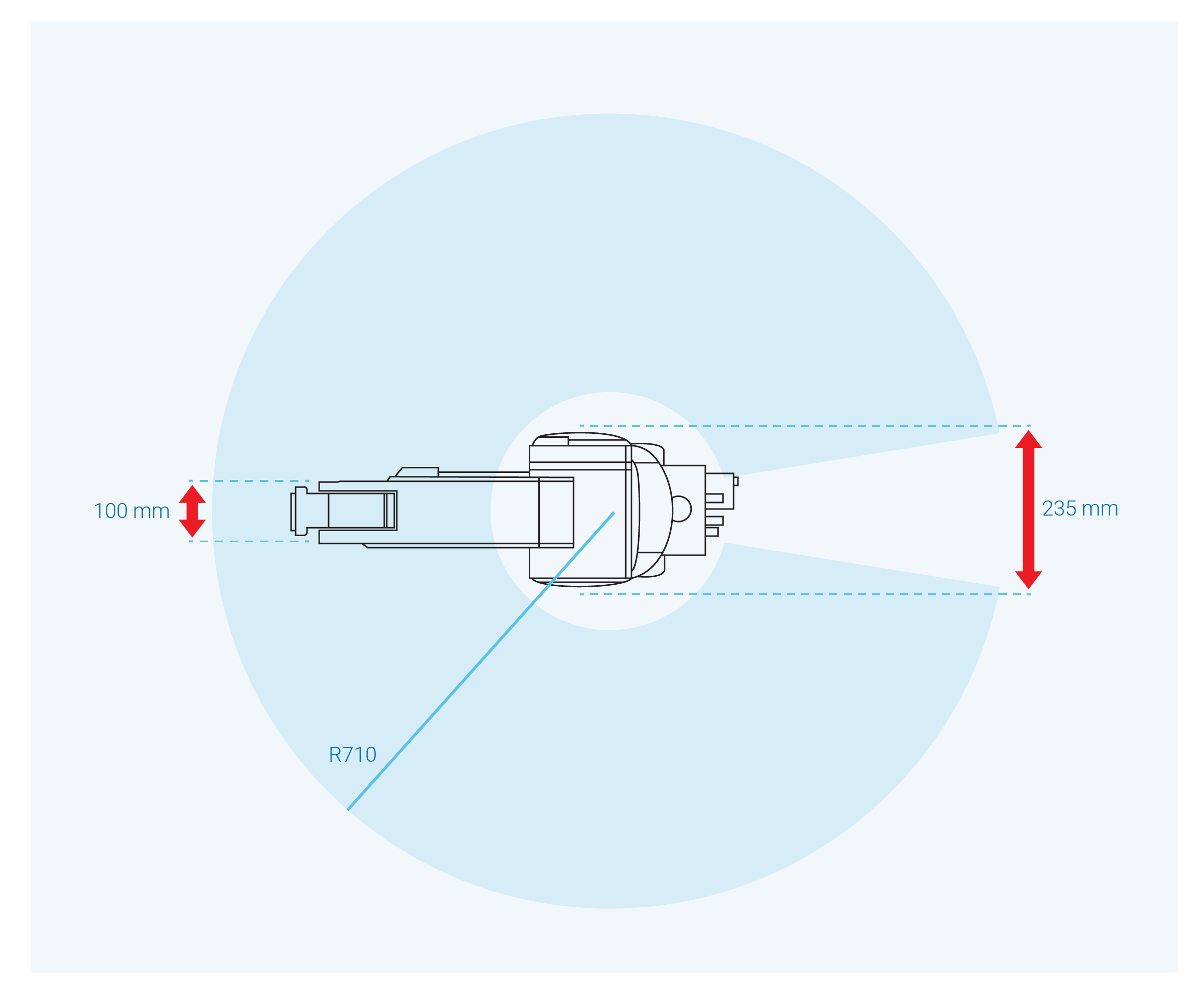
Powerful
- 7 kg payload in all directions, the highest in its class
- Adaptable to perform complex, massive hand or double hand movements in all directions without limitation
- Increased range of small robot applications in processes and improved flexibility in equipment and hand design
ANSI/CE Compliant
ANSI and CE compliant, making them suitable for global deployment.
Easy to Use
- A variety of installation methods
- World’s first embedded wiring
- Arm ends accommodate installation of camera, servo gripper, high density sensor array etc.
- Floor-, ceiling- or wall-mount is available
Built-in Wires
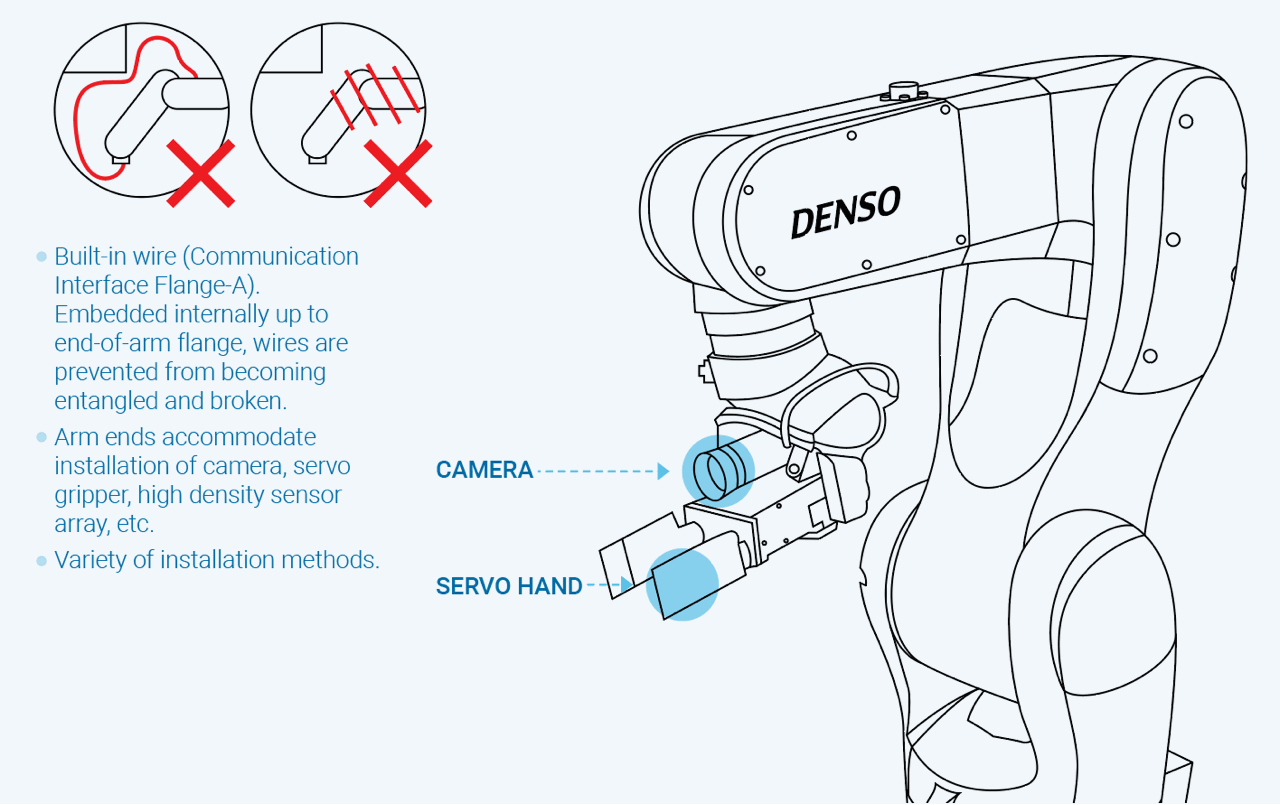
Environmental Resistance
- Protected type (IP67) for use in harsh environment
- Double-seal construction to exclude cutting fluid and chips
- Resistant to water-soluble cutting fluids
Options
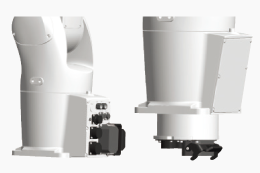
Connector Panel
Choose from two mounting orientations when connecting cables (motor and encoder cable, etc.) to the robot for increased flexibility to accommodate the robot installation conditions.
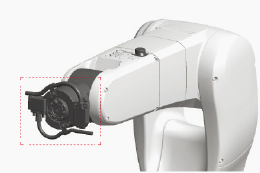
Flange
Plate mechanical interface has connectors for electrical signal lines and EtherNet, allowing wiring to be embedded in the robot unit.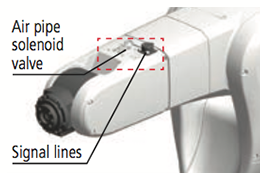
Signal Lines/Air Pipe Solenoid Valve
Signal lines and air pipe solenoid valves are embedded in the top of the second arm. Three varieties are available for VS-068/087 and one for VS-050/060.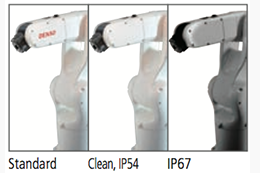
Paint and Surface Finish
If the protected type (IP67) is selected, the unit is left as aluminum. Standard paint is available in the special specification (option) when selecting IP67.
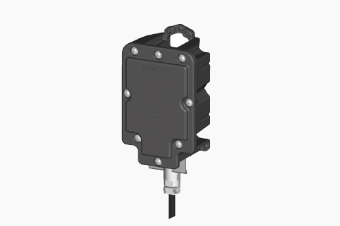
Battery Extension Unit
Encoder backup battery installed outside the robot facilitates easier battery replacement and overall maintenance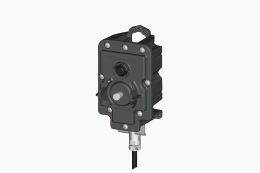
Brake Release Unit
A switch that allows you to release the brake of each axis. Wiring of this switch is connected directly to the brake release signal of each axis.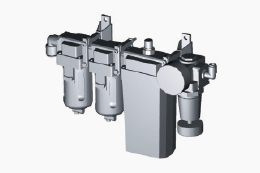
Air Purge Unit
The protected type (IP67) maintains an IP67 protection level by air pressure produced inside the robot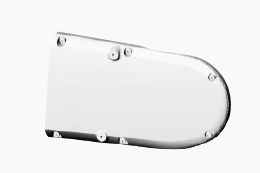
Second Arm Cover
This cover has tapped holes to secure wires for the robot’s second arm.Specifications
Standard Models
Model name | VS-050 | VS-060 | VS-068 | VS-087 | |
No. of axes | 6 | 6 | 6 | 6 | |
Position detection | Absolute encoder | Absolute encoder | Absolute encoder | Absolute encoder | |
Drive motor | AC servomotors for all joints | AC servomotors for all joints | AC servomotors for all joints | AC servomotors for all joints | |
Brakes | Brakes for all joints | Brakes for all joints | Brakes for all joints | Brakes for all joints | |
Overall arm length (first arm+second arm) | 505mm (250mm+255mm) | 605mm (305mm+300mm) | 680mm (340mm+340mm) | 875mm (445mm+430mm) |
|
Maximum motion area (Point P) | 505mm | 605mm | 710mm | 905mm | |
Motion range | J1 | ±170° *4 | ±170° *4 | ±170° *4 | ±170° *4 |
J2 | ±120° | ±120° | +135°, -100° | +135°, -100° | |
J3 | +151°, -120° | +155°, -25° | +153°, -120° | +153°, -136° | |
J4 | ±270° | ±270° | ±270° | ±270° | |
J5 | ±120° *5 | ±120° *5 | ±120° *5 | ±120° *5 | |
J6 | ±360° | ±360° | ±360° | ±360° | |
Maximum payload | 4kg | 4kg | 7kg | 7kg | |
Maximum composite speed at the center of an end-effector mounting face | 9,080mm/sec (RC8) 9,000mm/sec (RC7) | 9,390mm/sec (RC8) 9,000mm/sec (RC7) | 11,290mm/sec (RC8) 11,000mm/sec (RC7) | 11,380mm/sec (RC8) 11,000mm/sec (RC7) |
|
Cycle time *1 | 0.35 sec (RC8) 0.37 sec (RC7) | 0.35 sec (RC8) 0.37 sec (RC7) | 0.31 sec (RC8) 0.33 sec (RC7) | 0.34 sec (RC8) 0.36 sec (RC7) |
|
Position repeatability at the center of an end-effector mounting face *2 | ±0.02mm | ±0.02mm | ±0.02mm | ±0.03mm | |
Maximum allowable inertia moment(Inertia) | J4, J5 | 0.2kgm² | 0.2kgm² | 0.45kgm² | 0.45kgm² |
J6 | 0.05kgm² | 0.05kgm² | 0.1kgm² | 0.1kgm² | |
Maximum allowable moment | J4, J5 | 6.66 N•m | 6.66 N•m | 16.2 Nm | 16.2 Nm |
J6 | 3.13 N•m | 3.13 N•m | 6.86 Nm | 6.86 Nm | |
Signal line & air piping (optional) | Signal line | 10 (for proximity sensor signals, etc.) *6, 7 | 10 (for proximity sensor signals, etc.) *6, 7 | 10 (for proximity sensor signals, etc.) *6,7 | 10 (for proximity sensor signals, etc.) *6,7 |
Air Piping *3 | 5 systems (φ4x4, φ4x1) Solenoid Valve (2 Position, Double Solenoids) x2 | 5 systems (φ4x4, φ4x1) Solenoid Valve (2 Position, Double Solenoids) x2 | 7 systems (φ4x6, φ6x1) [solenoid valves can be selected from 1 to 3] 1. Solenoid Valve (2 Position, Double Solenoids) x3 2. Solenoid Valve (3 Position, Exhaust Center) x3 3. Solenoid Valve (3 Position, Closed Center) x3 | 7 systems (φ4x6, φ6x1) [solenoid valves can be selected from 1 to 3] 1. Solenoid Valve (2 Position, Double Solenoids) x3 2. Solenoid Valve (3 Position, Exhaust Center) x3 3. Solenoid Valve (3 Position, Closed Center) x3 |
|
Communication Interface Flange-A(optional) | 17 (power wire for cameras, etc.) *7 | 17 (power wire for cameras, etc.) *7 | 17 (power wire for cameras, etc.) *7 | 17 (power wire for cameras, etc.) *7 | |
LANx1(1000BASE-T) *8 | LANx1(1000BASE-T) *8 | LANx1(1000BASE-T) *8 | LANx1(1000BASE-T) *8 | ||
Air source | Operating pressure | 0.20 – 0.39 MPa | 0.20 – 0.39 MPa | 0.20 – 0.39 MPa | 0.20 – 0.39 MPa |
Maximum allowable pressure | 0.49 MPa | 0.49 MPa | 0.49 MPa | 0.49 MPa | |
Noise | <65 dB(A) | <65 dB(A) | <65 dB(A) | <65 dB(A) | |
IP classification | IP40 | IP40 | IP40 | IP40 | |
Approximate weight | 27kg | 28kg | 49kg | 51kg | |
*1Time required for a robot to move a 1kg payload between two points 300mm apart at a height of 25mm. | |||||
*2 Position repeatability is the precision at constant ambient temperature. | |||||
*3 For VS-050/060 - Controllable by use of the embedded solenoid valve only for φ4x4. For VS-068/087 - Controllable by use of the embedded solenoid valve only for φ4x6. | |||||
*4 Limited motion range when wall mounted. For details, please contact our sales representative. | |||||
*5 When communication interface flange-A is selected, the motion range of J5 is +120 and –110. | |||||
*6 There are 4 of these lines (proximity sensors or other signal lines) when selected together with communication interface flange-A. | |||||
*7 Allowable current is limited. | |||||
*8 The LAN cable to connect to the connector panel is 20m or shorter. | |||||
*9 Do not operate the robot in water. |
Dust & Splash Models
Model name | VS-050 | VS-060 | VS-068 | VS-087 | |
No. of axes | 6 | 6 | 6 | 6 | |
Position detection | Absolute encoder | Absolute encoder | Absolute encoder | Absolute encoder | |
Drive motor and brake | AC servomotors for all joints | AC servomotors for all joints | AC servomotors for all joints | AC servomotors for all joints | |
Brakes | Brakes for all joints | Brakes for all joints | Brakes for all joints | Brakes for all joints | |
Overall arm length (first arm+second arm) | 505mm (250mm+255mm) | 605mm (305mm+300mm) | 680mm (340mm+340mm) | 875mm (445mm+430mm) |
|
Maximum motion area (Point P) | 505mm | 605mm | 710mm | 905mm | |
Motion range | J1 | ±170° *4 | ±170° *4 | ±170° *4 | ±170° *4 |
J2 | ±120° | ±120° | +135°, -100° | +135°, -100° | |
J3 | +151°, -120° | +155°, -125° | +153°, -120° | +153°, -136° | |
J4 | ±270° | ±270° | ±270° | ±270° | |
J5 | ±120° | ±120° | ±120° | ±120° | |
J6 | ±360° | ±360° | ±360° | ±360° | |
Maximum payload | 4kg | 4kg | 7kg | 7kg | |
Maximum composite speed (at the center of an end-effector mounting face) | 9,080mm/sec (RC8) 9,000mm/sec (RC7) | 9,390mm/sec (RC8) 9,000mm/sec (RC7) | 11,000mm/sec | 11,000mm/sec | |
Cycle time *1 | 0.35 sec (RC8) 0.37 sec (RC7) | 0.35 sec (RC8) 0.37 sec (RC7) | 0.33 sec | 0.36 sec | |
Position repeatability at the center of an end-effector mounting face *2 | ±0.02 sec | ±0.02 sec | ±0.02mm | ±0.03mm | |
Maximum allowable inertia moment (inertia) | J4, J5 | 0.2kmg² | 0.2kmg² | 0.45kgm² | 0.45kgm² |
J6 | 0.05kmg² | 0.05kmg² | 0.1kgm² | 0.1kgm² | |
Maximum allowable moment | J4, J5 | 6.66 N•m | 6.66 N•m | 16.2 N•m | 16.2 N•m |
J6 | 3.13 N•m | 3.13 N•m | 6.86 N•m | 6.86 N•m | |
Signal line & air piping (optional) | Signal line | 10 (for proximity sensor signals, etc.) *5 | 10 (for proximity sensor signals, etc.) *5 | 10 (for proximity sensor signals, etc.) *5 | 10 (for proximity sensor signals, etc.) *5 |
Air Piping *3 | 5 systems (φ4x4, φ4x1) Solenoid Valve (2 Position, Double Solenoids) x2 | 5 systems (φ4x4, φ4x1) Solenoid Valve (2 Position, Double Solenoids) x2 | 7 systems (φ4x6, φ6x1) [solenoid valves can be selected from 1 to 3] 1. Solenoid Valve (2 Position, Double Solenoids) x3 2. Solenoid Valve (3 Position, Exhaust Center) x3 3. Solenoid Valve (3 Position, Closed Center) x3 | 7 systems (φ4x6, φ6x1) [solenoid valves can be selected from 1 to 3] 1. Solenoid Valve (2 Position, Double Solenoids) x3 2. Solenoid Valve (3 Position, Exhaust Center) x3 3. Solenoid Valve (3 Position, Closed Center) x3 |
|
Air source | Operating pressure | 0.20 - 0.39 MPa | 0.20 - 0.39 MPa | 0.20 - 0.39 MPa | 0.20 - 0.39 MPa |
Maximum allowable pressure | 0.49 MPa | 0.49 MPa | 0.49 MPa | 0.49 MPa | |
Noise | <65 dB(A) | <65 dB(A) | <65 dB(A) | <65 dB(A) | |
IP classification | IP54, Wrist: IP65) | IP54, Wrist: IP65) | Unit: IP54, Wrist: IP65 | Unit: IP54, Wrist: IP65 | |
Approximate weight | 27kg | 28kg | 49kg | 51kg | |
*1 Time required for a robot to move a 1kg payload between two points 300mm apart at a height of 25mm. | |||||
*2 Position repeatability is the precision at constant ambient temperature. | |||||
*3 Controllable by use of the embedded solenoid valve only for φ4x4. | |||||
*4 Limited motion range when wall mounted. For details, please contact our sales representative. | |||||
*5 Allowable current is limited. |
ISO 3 Cleanroom Models
Model name | VS-050 | VS-060 | VS-068 | VS-087 | |
No. of axes | 6 | 6 | 6 | 6 | |
Position detection | Absolute encoder | Absolute encoder | Absolute encoder | Absolute encoder | |
Drive motor | AC servomotors for all joints | AC servomotors for all joints | AC servomotors for all joints | AC servomotors for all joints | |
Brakes | Brakes for all joints | Brakes for all joints | Brakes for all joints | Brakes for all joints | |
Overall arm length (first arm+second arm) | 505mm (250mm+255mm) | 605mm (305mm+300mm) | 680mm (340mm+340mm) | 875mm (445mm+430mm) |
|
Maximum motion area (Point P) | 505mm | 605mm | 710mm | 905mm | |
Motion range | J1 | ±170 | ±170 | ±170° | ±170° |
J2 | ±120° | ±120° | +135°, -100° | +135°, -100° | |
J3 | +151°, -120° | +155°, -125° | +153°, -120° | +153°, -136° | |
J4 | ±270° | ±270° | ±270° | ±270° | |
J5 | ±120° | ±120° | ±120° | ±120° | |
J6 | ±360° | ±360° | ±360° | ±360° | |
Maximum payload | 4kg | 4kg | 7kg | 7kg | |
Maximum composite speed(at the center of an end-effector mounting face) | 9,080mm (RC8) 9,000mm (RC7) | 9,390mm (RC8) 9,000mm (RC7) | 11,000mm/sec | 11,000mm/sec | |
Cycle time *1 | 0.35 sec (RC8) 0.37 sec (RC7) | 0.35 sec (RC8) 0.37 sec (RC7) | 0.33 sec | 0.36 sec | |
Position repeatability at the center of an end-effector mounting face *2 | ±0.02 sec | ±0.02 sec | ±0.02mm | ±0.03mm | |
Maximum allowable moment of inertia | J4, J5 | 0.2kmg² | 0.2kmg² | 0.45kgm² | 0.45kgm² |
J6 | 0.05kmg² | 0.05kmg² | 0.1kgm² | 0.1kgm² | |
Maximum allowable moment | J4, J5 | 6.66 N•m | 6.66 N•m | 16.2 N•m | 16.2 N•m |
J6 | 3.13 N•m | 3.13 N•m | 6.86 N•m | 6.86 N•m | |
Signal line & air piping (optional) | Signal line | 10 (for proximity sensor signals, etc.) *4 | 10 (for proximity sensor signals, etc.) *4 | 10 (for proximity sensor signals, etc.) *4 | 10 (for proximity sensor signals, etc.) *4 |
Air Piping *3 | 5 systems (φ4x4, φ4x1) Solenoid Valve (2 Position, Double Solenoids) x2 | 5 systems (φ4x4, φ4x1) Solenoid Valve (2 Position, Double Solenoids) x2 | 6 systems (φ4x6) [solenoid valves can be selected from 1 to 3] 1. Solenoid Valve (2 Position, Double Solenoids) x3 2. Solenoid Valve (3 Position, Exhaust Center) x3 3. Solenoid Valve (3 Position, Closed Center) x3 | 6 systems (φ4x6) [solenoid valves can be selected from 1 to 3] 1. Solenoid Valve (2 Position, Double Solenoids) x3 2. Solenoid Valve (3 Position, Exhaust Center) x3 3. Solenoid Valve (3 Position, Closed Center) x3 |
|
Air source | Operating pressure | 0.20 - 0.39 MPa | 0.20 - 0.39 MPa | 0.20 - 0.39 MPa | 0.20 - 0.39 MPa |
Maximum allowable pressure | 0.49 MPa | 0.49 MPa | 0.49 MPa | 0.49 MPa | |
Noise | <65 dB(A) | <65 dB(A) | <65 dB(A) | <65 dB(A) | |
Cleanroom classification (ISO14644-1) | ISO 3 | ISO 3 | ISO 3 | ISO 3 | |
Approximate Weight | 27kg | 28kg | 49kg | 51kg | |
*1 Time required for a robot to move a 1kg payload between two points 300mm apart at a height of 25mm. | |||||
*2 Position repeatability is the precision at constant ambient temperature. | |||||
*3 For VS-050/060 - Controllable by use of the embedded solenoid valve only for φ4x4. For VS-068/087 - Controllable by use of the embedded solenoid valve only for φ4×6. | |||||
*4 Allowable current is limited. |
ISO 5 Cleanroom Models
Model name | VS-050 | VS-060 | VS-068 | VS-087 | |
No. of axes | 6 | 6 | 6 | 6 | |
Position detection | Absolute encoder | Absolute encoder | Absolute encoder | Absolute encoder | |
Drive motor | AC servomotors for all joints | AC servomotors for all joints | AC servomotors for all joints | AC servomotors for all joints | |
Brakes | Brakes for all joints | Brakes for all joints | Brakes for all joints | Brakes for all joints | |
Overall arm length (first arm+second arm) | 505mm (250mm+255mm) | 605mm (305mm+300mm) | 680mm (340mm+340mm) | 875mm (445mm+430mm) |
|
Maximum motion area (Point P) | 505mm | 605mm | 710mm | 905mm | |
Motion range | J1 | ±170° | ±170° | ±170° | ±170° |
J2 | ±120° | ±120° | +135°, -100° | +135°, -100° | |
J3 | +151°, -120° | +155°, -125° | +153°, -120° | +153°, -136° | |
J4 | ±270° | ±270° | ±270° | ±270° | |
J5 | ±120° | ±120° | ±120° | ±120° | |
J6 | ±360° | ±360° | ±360° | ±360° | |
Maximum payload | 4kg | 4kg | 7kg | 7kg | |
Maximum composite speed(at the center of an end-effector mounting face) | 9,080mm/sec (RC8) 9,000mm/sec (RC7) | 9,390mm/sec (RC8) 9,000mm/sec (RC7) | 11,000mm/sec | 11,000mm/sec | |
Cycle time *1 | 0.35 sec (RC8) 0.37 sec (RC7) | 0.35 sec (RC8) 0.37sec (RC7) | 0.33 sec | 0.36 sec | |
Position repeatability(at the center of an end-effector mounting face) *2 | ±0.02mm | ±0.02mm | ±0.02mm | ±0.03mm | |
Maximum allowable moment of inertia | J4, J5 | 0.2kgm² | 0.2kgm² | 0.45kgm² | 0.45kgm² |
J6 | 0.05kgm² | 0.05kgm² | 0.1kgm² | 0.1kgm² | |
Maximum allowable moment | J4, J5 | 6.66 N•m | 6.66 N•m | 16.2 N•m | 16.2 N•m |
J6 | 3.13 N•m | 3.13 N•m | 6.86 N•m | 6.86 N•m | |
Signal line & air piping (optional) | Signal line | 10 (for proximity sensor signals, etc.) *4 | 10 (for proximity sensor signals, etc.) *4 | 10 (for proximity sensor signals, etc.) *4 | 10 (for proximity sensor signals, etc.) *4 |
Air Piping *3 | 4 systems (φ4x4) Solenoid Valve (2 Position, Double Solenoids) x2 | 4 systems (φ4x4) Solenoid Valve (2 Position, Double Solenoids) x2 | 6 systems (φ4x6) [solenoid valves can be selected from 1 to 3] 1. Solenoid Valve (2 Position, Double Solenoids) x3 2. Solenoid Valve (3 Position, Exhaust Center) x3 3. Solenoid Valve (3 Position, Closed Center) x3 | 6 systems (φ4x6) [solenoid valves can be selected from 1 to 3] 1. Solenoid Valve (2 Position, Double Solenoids) x3 2. Solenoid Valve (3 Position, Exhaust Center) x3 3. Solenoid Valve (3 Position, Closed Center) x3 |
|
Air source | Operating pressure | 0.20 - 0.39 MPa | 0.20 - 0.39 MPa | 0.20 - 0.39 MPa | 0.20 - 0.39 MPa |
Maximum allowable pressure | 0.49 MPa | 0.49 MPa | 0.49 MPa | 0.49 MPa | |
Noise | <65 dB(A) | <65 dB(A) | <65 dB(A) | <65 dB(A) | |
Cleanroom classification (ISO14644-1) | ISO 5 | ISO 5 | ISO 5 | ISO 5 | |
Approximate weight | 27kg | 28kg | 49kg | 51kg | |
*1 Time required for a robot to move a 1kg payload between two points 300mm apart at a height of 25mm. | |||||
*2 Position repeatability is the precision at constant ambient temperature. | |||||
*3 For 050/060 - Controllable by use of the embedded solenoid valve only for φ4x4. For 068/087 - Controllable by use of the embedded solenoid valve only for φ4×6. | |||||
*4 Allowable current is limited. |
IP67 Models
Model name | VS-050 | VS-060 | VS-068 | VS-087 | |
No. of axes | 6 | 6 | 6 | 6 | |
Position detection | Absolute encoder | Absolute encoder | Absolute encoder | Absolute encoder | |
Drive motor | AC servomotors for all joints | AC servomotors for all joints | AC servomotors for all joints | AC servomotors for all joints | |
Brakes | Brakes for all joints | Brakes for all joints | Brakes for all joints | Brakes for all joints | |
Overall arm length (first arm+second arm) | 505mm (250mm+255mm) | 605mm (305mm+300mm) | 680mm (340mm+340mm) | 875mm (445mm+430mm) |
|
Maximum motion area (Point P) | 505mm | 605mm | 710mm | 905mm | |
Motion range | J1 | ±170° *4 | ±170° *4 | ±170° *4 | ±170° *4 |
J2 | ±120° | ±120° | +135°, -100° | +135°, -100° | |
J3 | +151°, -120° | °+155°, -125° | +153°, -120° | +153°, -136° | |
J4 | ±270° | ±270° | ±270° | ±270° | |
J5 | ±120° | ±120° | ±120° | ±120° | |
J6 | ±360° | ±360° | ±360° | ±360° | |
Maximum payload | 4kg | 4kg | 7kg | 7kg | |
Maximum composite speed (at the center of an end-effector mounting face) | 9,080mm/sec (RC8) 9,000mm/sec (RC7) | 9,390mm/sec (RC8) 9,000mm/sec (RC7) | 11,000mm/sec | 11,000mm/sec | |
Cycle time *1 | 0.35 sec (RC8) 0.37 sec (RC7) | 0.35 sec (RC8) 0.37 sec (RC7) | 0.33 sec | 0.36 sec | |
Position repeatability (at the center of an end-effector mounting face) *2 | ±0.02mm | ±0.02mm | ±0.02mm | ±0.03mm | |
Maximum allowable moment of inertia | J4, J5 | 0.2kgm² | 0.2kgm² | 0.45kgm² | 0.45kgm² |
J6 | 0.05kgm² | 0.05kgm² | 0.1kgm² | 0.1kgm² | |
Maximum allowable moment | J4, J5 | 6.66 N•m | 6.66 N•m | 16.2 N•m | 16.2 N•m |
J6 | 3.13 N•m | 3.13 N•m | 6.86 N•m | 6.86 N•m | |
Signal line & air piping (optional) | Signal line | 10 (for proximity sensor signals, etc.) *6 | 10 (for proximity sensor signals, etc.) *6 | 10 (for proximity sensor signals, etc.) *5,6 | 10 (for proximity sensor signals, etc.) *5,6 |
Air Piping *3 | 5 systems (φ4x4, φ4x1) Solenoid Valve (2 Position, Double Solenoids) x2 | 5 systems (φ4x4, φ4x1) Solenoid Valve (2 Position, Double Solenoids) x2 | 7 systems (φ4x6, φ6x1) [solenoid valves can be selected from 1 to 3] 1. Solenoid Valve (2 Position, Double Solenoids) x3 2. Solenoid Valve (3 Position, Exhaust Center) x3 3. Solenoid Valve (3 Position, Closed Center) x3 | 7 systems (φ4x6, φ6x1) [solenoid valves can be selected from 1 to 3] 1. Solenoid Valve (2 Position, Double Solenoids) x3 2. Solenoid Valve (3 Position, Exhaust Center) x3 3. Solenoid Valve (3 Position, Closed Center) x3 |
|
Communication Interface Flange-A (optional) | 17 (power wire for cameras, etc.) *6 | 17 (power wire for cameras, etc.) *6 | 17 (power wire for cameras, etc.) *6 | 17 (power wire for cameras, etc.) *6 | |
LANx1(1000BASE-T) *7 | LANx1(1000BASE-T) *7 | LANx1(1000BASE-T) *7 | LANx1(1000BASE-T) *7 | ||
Air source | Operating pressure | 0.20 – 0.39 MPa | 0.20 – 0.39 MPa | 0.20 – 0.39 MPa | 0.20 – 0.39 MPa |
Maximum allowable pressure | 0.49 MPa | 0.49 MPa | 0.49 MPa | 0.49 MPa | |
Noise | <65 dB(A) | <65 dB(A) | <65 dB(A) | <65 dB(A) | |
IP classification | IP67 *8 | IP67 *8 | IP67 *8 | IP67 *8 | |
Approximate weight | 27kg | 28kg | 49kg | 51kg | |
*1 Time required for a robot to move a 1kg payload between two points 300mm apart at a height of 25mm. | |||||
*2 Position repeatability is the precision at constant ambient temperature. | |||||
*3 Controllable by use of the embedded solenoid valve only for φ4x4. | |||||
*4 Limited motion range when wall mounted. For details, please contact our sales representative. | |||||
*5 There are 4 of these lines (proximity sensors or other signal lines) when selected together with communication interface flange-A. | |||||
*6 Allowable current is limited. | |||||
*7 The LAN cable to connect to the connector panel is 20 m or shorter. | |||||
*8 Do not operate the robot in water. |
Downloads
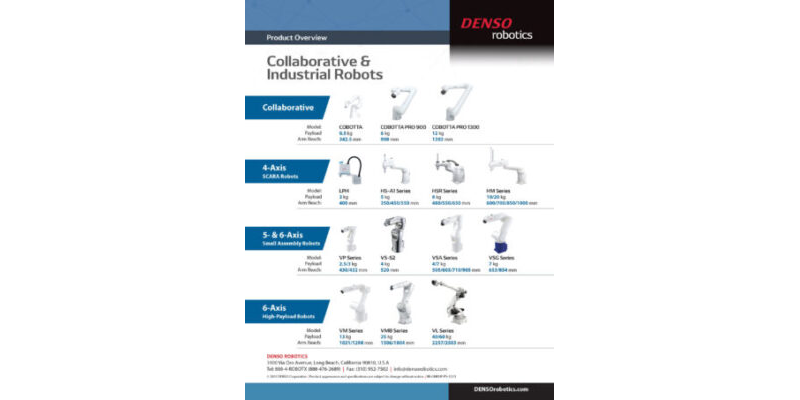
Collaborative & Industrial Robots Lineup Card
- Version
- Download 0
- File Size 4.00 KB
- File Count 1
- Create Date May 1, 2025
- Last Updated May 1, 2025
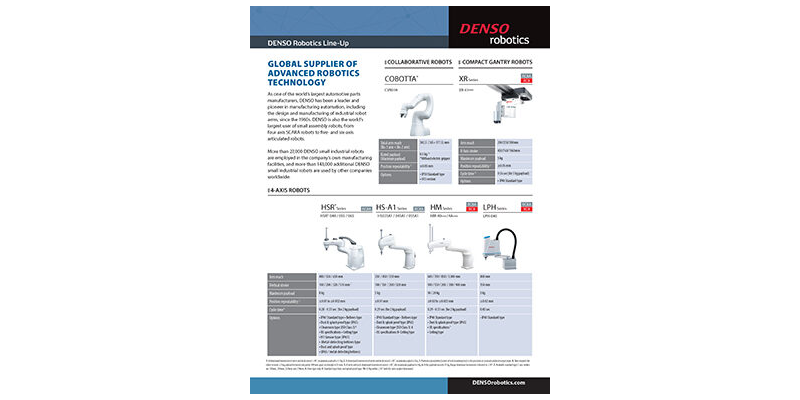
Robot Series Product Sheet
Overview of all DENSO robots
- Version
- Download 1355
- File Size 0.00 KB
- File Count 1
- Create Date June 9, 2022
- Last Updated January 16, 2024
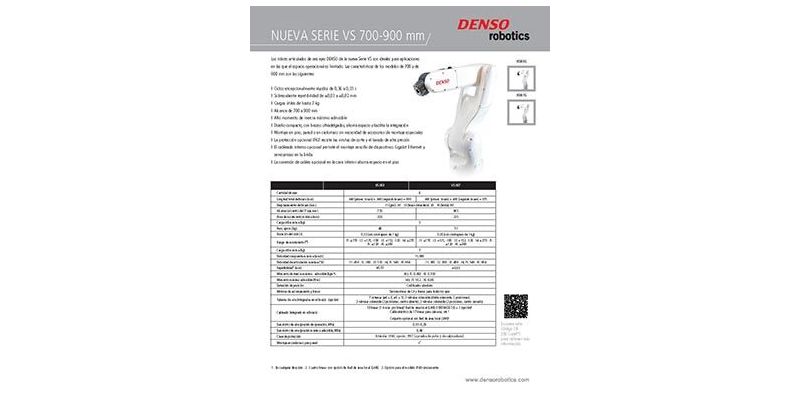
Hoja de producto de la serie VSA 068-087 (Spanish)
Ficha de producto de dos páginas con características, especificaciones y dimensiones.
- Version
- Download 44
- File Size 0.00 KB
- File Count 1
- Create Date October 15, 2021
- Last Updated June 9, 2022
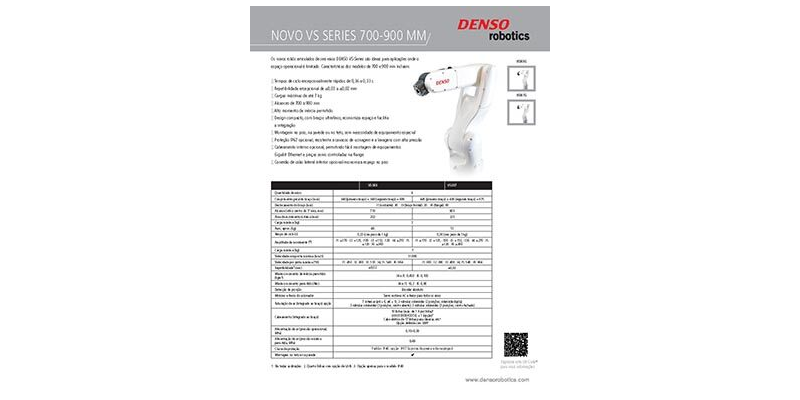
Folha de produto da série VSA 068-087 (Portuguese)
Folha de produto de duas páginas com características, especificações e dimensões.
- Version
- Download 17
- File Size 0.00 KB
- File Count 1
- Create Date October 15, 2021
- Last Updated June 9, 2022
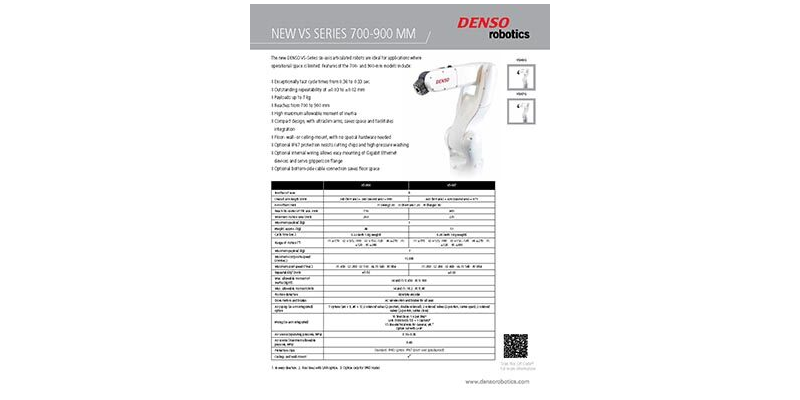
VSA 068 087 Series Product Sheet
Two-page product sheet with features, specifications and dimensions.
- Version
- Download 166
- File Size 0.00 KB
- File Count 1
- Create Date October 15, 2021
- Last Updated June 9, 2022
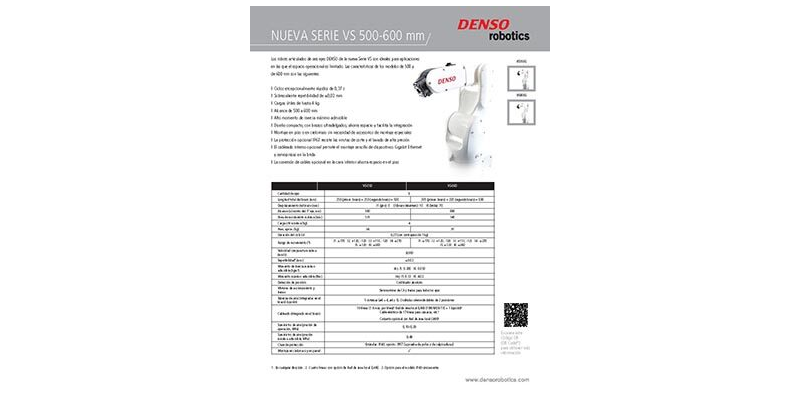
Hoja de producto de la serie VSA 050-060 (Spanish)
Ficha de producto de dos páginas con características, especificaciones y dimensiones.
- Version
- Download 12
- File Size 0.00 KB
- File Count 1
- Create Date October 15, 2021
- Last Updated June 9, 2022
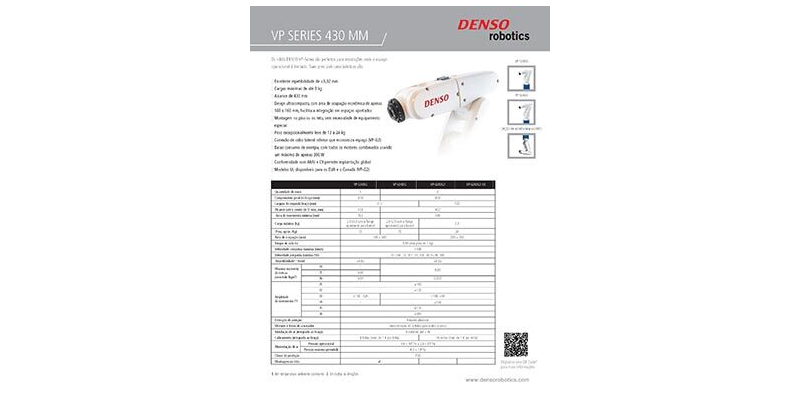
Folha de produto da série VSA 050-060 (Portuguese)
Folha de produto de duas páginas com características, especificações e dimensões.
- Version
- Download 10
- File Size 0.00 KB
- File Count 1
- Create Date October 15, 2021
- Last Updated June 9, 2022
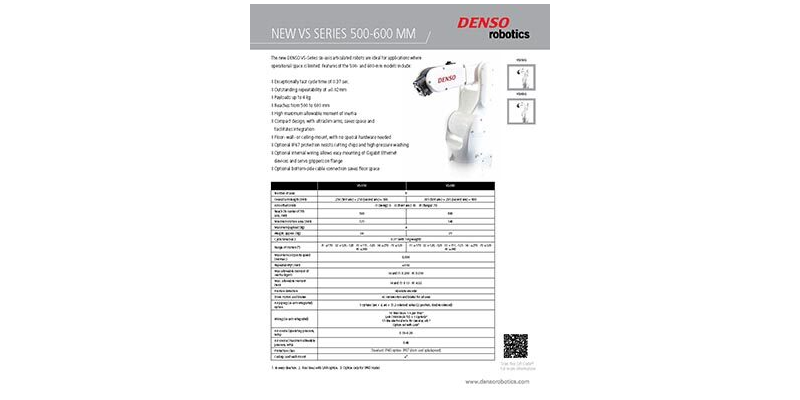
VSA 050 060 Series Product Sheet
Two-page product sheet with features, specifications and dimensions.
- Version
- Download 112
- File Size 0.00 KB
- File Count 1
- Create Date October 15, 2021
- Last Updated June 9, 2022
CAD Files and Manuals
Find 2D/3D CAD data, application software, PDF manuals, and part lists. (Account registration required)
Online/Interactive Manuals
Account registration required.